2015 OPEN HOUSE in HERBORN (Germany)
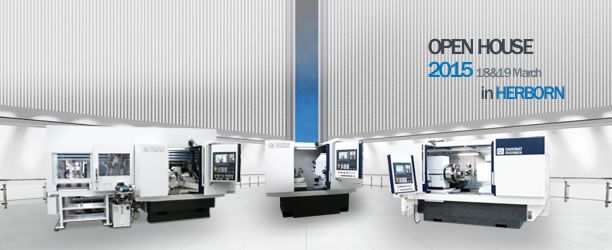
DANOBATGROUP is holding its 2015 OPEN HOUSE on the 18th and 19th of March at its manufacturing plant in Herborn (Germany).
The OPEN HOUSE will provide the opportunity to showcase the technology behind DANOBAT and DANOBAT-OVERBECKmachines, and the new developments applied to its wide range of grinding machines. Some of these developments will be showcased in real machining conditions, by the best specialists in these technologies.
DANOBATGROUP is holding its 2015 OPEN HOUSE on the 18th and 19th of March at its manufacturing plant in Herborn (Germany).
The OPEN HOUSE will provide the opportunity to showcase the technology behind DANOBAT and DANOBAT-OVERBECKmachines, and the new developments applied to its wide range of grinding machines. Some of these developments will be showcased in real machining conditions, by the best specialists in these technologies.
The company´s strategy is not merely to develop machines, but also solutions for the machining of high value-added complex components. These solutions consist of machines, accessories, tools and more. Therefore, the company will not just be exhibiting machines, but also complete tailor-made solutions. These solutions have been developed to create value for customers who are market leaders in their sectors.
The visit will consist of a guided tour of the company´s facilities to discover their ambitious project based on cutting edge technology, knowledge, innovation and advanced solutions. In addition, select suppliers will present their products while providing information on related issues.
Among many other machines, the firm will exhibit the DANOBAT-OVERBECK IRD-400 internal and radius model and the DANOBAT LG-400 external grinding machine.
The DANOBAT-OVERBECK IRD-400 belongs to the three-model IRD range of high precision grinding machines for internal, external, radius, face and non-circular grinding. With a maximum internal grinding diameter of 200 mm, its workpiece swing diameter is 400 mm and maximum workpiece weight is between 70 and 170 kg.
Ideally suited for the machining of dies and punches, for example, the integrated B axis of the workhead, with a swivel range of +95º/-15º, is combined with 3-axis interpolative software to allow the grinding of different radii without manual re-setting of the pivot points. The T-slide configuration (400 mm X axis travel/400 mm Z axis travel) contributes to a compact machine design. Both slide elements are characterised by fast traverse speed, precise positioning and low maintenance requirements.
The direct driven workhead ensures the highest possible roundness quality, while contributing to flexibility and short change-over times. Up to 4 grinding spindles plus a measuring probe can be mounted on the wheelhead. Both high frequency and belt-driven spindles can be used.
The new development of the cam grinding software offers the possibility to grind basic non-circular shapes in combination with a freely-defined workpiece profile. Furthermore, shapes can be ground that require non-continuous circulation of the workhead spindle, e.g. bores outside the workpiece rotation center.
In the field of external grinding machines, a DANOBAT LG-400 grinding machine will also be on display. The LG grinding machine range offers excellent results in the high precision machining of small parts, such as cutting tools, ultra-precision parts for the hydraulics industry, parts for the automotive sector, etc.
The LG-400 is an intermediate model within the LG grinding machine range that allows parts with a maximum diameter of 300 mm to be machined with a maximum grinding length of 400 mm, while the top-of-the-range model accepts parts of up to 300 mm in diameter, with a grinding length of 600 mm.
The machine has been equipped with a robot and a pallet loading and unloading system. This system (and others that can be included with this model, i.e. gantry, conveyor, etc.) permits much shorter part change times, which are typically between 2-6 seconds.
The machine also has a multi-wheel B axis equipped with grinding heads that allow the use of wheels of up to 500 mm x 80 mm. The wheels may be conventional, superabrasive or a combination of both technologies, thus increasing production capacity and improving the final quality of the parts.
Slides are driven by means of linear motors fitted on preloaded bearings, while the wheel head is operated by means of a cooled electro-spindle that permits a large range of peripheral speeds with maximum torque. These drive systems, together with the bed manufactured from natural granite for the absorption of vibrations, give the entire assembly the rigidity and stability necessary for achieving excellent precision.
DANOBAT LG range offers the latest technology with a modern and ergonomic design that allows the machine to be adapted to the needs of each customer, with options such as automatic loading/unloading systems, multi-wheel B axis, synchronised tailstock, a follow-rest (facing the wheel), different types of diamond dressing tools (radius, crush, wheel), etc.