DANOBAT presents its latest developments at BIEMH exhibition
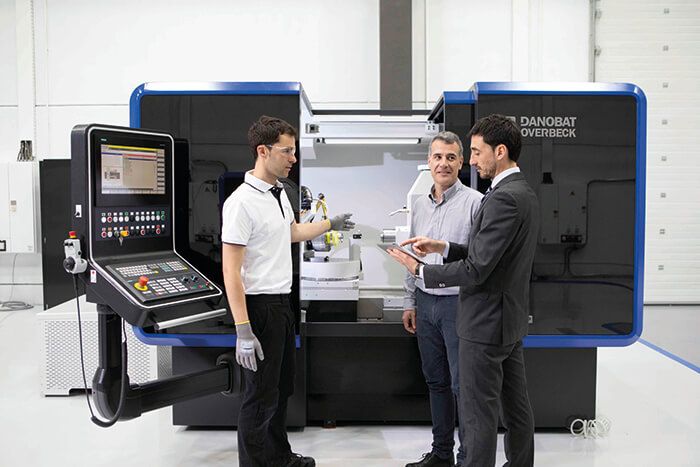
DANOBAT will participate at BIEMH (Hall 5 - Stand C/03), from May 28th to June 1st, exhibiting the latest advanced solutions as well as its focus on industrial digitalisation.
During the fair, DANOBAT will present the IRD-400, an internal, external, surface and radius grinding machine developed by the its subsidiary in Germany, DANOBAT-OVERBECK. This machine is specially designed for high precision components.
In addition, the company will avail of this opportunity to share its digital value proposition, composed of in-house technological developments based on industry 4.0 concepts with an aim to advancing in the creation of intelligent manufacturing spaces, fitted with interconnected equipment and capable of autonomous operation.
A solution for non-cylindrical shapes and radii
The IRD-400 grinding solution offer which the company intends to take to the fair includes internal, external, surface and radius grinding, a solution especially designed for machining dies and moulds.
The main advantages offered by this development are the maximum precision results obtained for pieces with high geometric complexity and with high productivity.
The grinding machine achieves highly accurate finishes thanks to its B0 axis which swivels up to 91 degrees. Axis control means complex internal shapes can be made using one single wheel and in one contour line, thus maximizing productivity.
With this model, the 4-spindle turret includes a measuring probe integrated in the software with which the starting position of the workpiece can be detected. This ensures that, on the final finishing run, the system reaches the required measurement with precision. In round contours, roundness deviations of 0.5 µm can be reached.
Another of the peculiarities of this development is the high degree of exact synchronisation of all the movements of the axes, including the rotation axis of the workpiece (C0), thus enabling eccentric grinding. This feature means that complex geometries can also be machined with the aid of coordinate grinding, and square, rectangular or freeform shapes can be made to great precision.
4.0 technologies for the automation of real manufacturing environments
DANOBAT will show its commitment to digitalisation at the fair. With the aim of improving in the construction of intelligent manufacturing spaces, equipped with interconnected machines and with the capacity to work autonomously, it has a value proposition composed of self-developed solutions based on the latest advances in digital technology.
DANOBAT will likewise explain its focus on industrial digitalisation, which is structured around an offer of intelligent developments using 4.0 technologies, with an aim to forging ahead in the automation of real manufacturing environments.
Among its intelligent developments equipped with 4.0 technologies, DANOBAT offers the Smart HMI, an intuitive interface aiding the operator and facilitating the use of the machinery, thus raising productivity.
The Data System focuses on the development of a platform for capturing, storing and processing data with means the status of the monitored machine.
The Control System, enables the control, monitoring and supervision of data of all the stages of the machining process in high complexity manufacturing lines, made up of different machines and equipment.
A solution for non-cylindrical shapes and radii
The IRD-400 grinding solution offer which the company intends to take to the fair includes internal, external, surface and radius grinding, a solution especially designed for machining dies and moulds.
The main advantages offered by this development are the maximum precision results obtained for pieces with high geometric complexity and with high productivity.
The grinding machine achieves highly accurate finishes thanks to its B0 axis which swivels up to 91 degrees. Axis control means complex internal shapes can be made using one single wheel and in one contour line, thus maximizing productivity.
With this model, the 4-spindle turret includes a measuring probe integrated in the software with which the starting position of the workpiece can be detected. This ensures that, on the final finishing run, the system reaches the required measurement with precision. In round contours, roundness deviations of 0.5 µm can be reached.
Another of the peculiarities of this development is the high degree of exact synchronisation of all the movements of the axes, including the rotation axis of the workpiece (C0), thus enabling eccentric grinding. This feature means that complex geometries can also be machined with the aid of coordinate grinding, and square, rectangular or freeform shapes can be made to great precision.
4.0 technologies for the automation of real manufacturing environments
DANOBAT will show its commitment to digitalisation at the fair. With the aim of improving in the construction of intelligent manufacturing spaces, equipped with interconnected machines and with the capacity to work autonomously, it has a value proposition composed of self-developed solutions based on the latest advances in digital technology.
DANOBAT will likewise explain its focus on industrial digitalisation, which is structured around an offer of intelligent developments using 4.0 technologies, with an aim to forging ahead in the automation of real manufacturing environments.
Among its intelligent developments equipped with 4.0 technologies, DANOBAT offers the Smart HMI, an intuitive interface aiding the operator and facilitating the use of the machinery, thus raising productivity.
The Data System focuses on the development of a platform for capturing, storing and processing data with means the status of the monitored machine.
The Control System, enables the control, monitoring and supervision of data of all the stages of the machining process in high complexity manufacturing lines, made up of different machines and equipment.