DANOBAT showcases its focus on industrial digitalisation and the development of advanced manufacturing solutions at EMO in Hannover
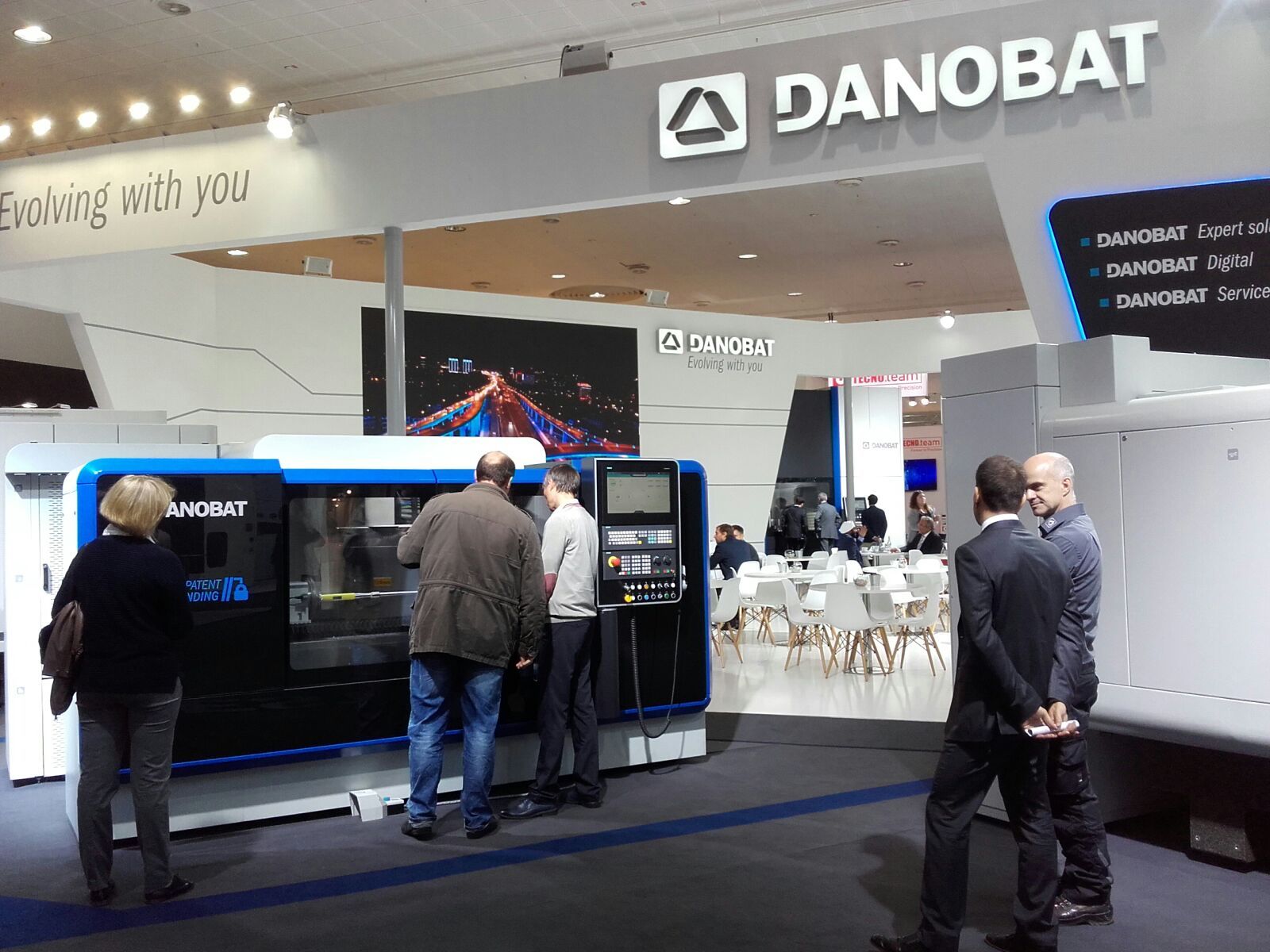
-
The machine tool and production system manufacturer will have a strong representation at the fair, to be held from 18 to 23 September in the German city
-
The company will have an 800 square metre stand to present its new grinding and turning solutions and exhibit innovative developments completely redesigned to guarantee ultra-precision results
-
The company will likewise lay out its digital value proposition, made up of its in-house developed technologies within the industry 4.0 paradigm
-
DANOBAT will present its service offer aimed at adding value to machinery and guaranteeing optimum operation for the useful life of its machines
With an aim to advertising its firm stake in the development of innovative manufacturing solutions and its digital value proposition, the machine tool and production system manufacturer, DANOBAT will have a strong representation at the coming edition of the EMO fair in Hannover. At the event, the company will launch three completely new developments, present its range of redesigned machines for maximum-precision grinding and turning and will publicise its high added value service offer.
One of the most important fairs for the industrial manufacturing sector in Europe, the event will serve as the showcase for the company to display the solutions designed for carrying out high productivity grinding and turning processes of great technical complexity.
In addition, the company will avail of this opportunity to share its digital value proposition, composed of in-house technological developments based on industry 4.0 concepts with an aim to advancing in the creation of intelligent manufacturing spaces, fitted with interconnected equipment and capable of autonomous operation.
DANOBAT, which will have its own exhibition space of 800 square metres (stand C-45, Hall 11), will likewise present its advanced service offer aimed at offering intelligent machine management, adding value to machinery, improving maintenance strategies and optimising performance and production.
The company, which is strongly internationalised, also intends to reveal its plans to reinforce its presence in Italy, which stands out for its high degree of competitiveness, and is a priority market in the company’s strategy.
With over 2,100 exhibitors and a surface area of 180,000 square metres, the EMO fair will be held in the German city of Hannover from 18 to 23 September.
Below are the technologically advanced developments that DANOBAT is to present at the coming edition of the fair:
1. Maximum rigidity centreless grinding
DANOBAT will present the ESTARTA-650 centreless grinding machine, a completely new solution characterised by being one of the most rigid grinding machines of these characteristics on the market.
The ESTARTA-650 was designed to meet current high-speed manufacturing demands for the purpose of significantly improving the cycle times and maximising production.
The main advantages of this solution are its high precision, a 30% rise in productivity and great rigidity.
This development can achieve 120 metres per second in throughfeed minimising the generation of vibrations. This characteristic -working at great speeds with maximum vibration absorption- is a key feature for successfully carrying out highly demanding grinding processes.
The grinding machine is fitted with linear motors, a granite bed, a drive head fitted with an additional support that does away with the cantilever, and a novel damping system.
The solution also has a rolling guide system, affording it greater sensitivity in movement. This last feature implies the elimination of the hydraulic component, making the ESTARTA-650 an environment-friendly sustainable grinding machine, requiring less consumption and maintenance.
2. High precision for hard turning
Another of the solutions that DANOBAT intends to take to EMO is the high-precision turning machine for hard turning, the LT-400, a development which is characterised by achieving maximum quality results with great flexibility and adaptability to the client’s needs.
The LT-400 adjusts perfectly to the demands of short-run manufacturers, who are required to frequently modify the type of parts they manufacture, without needing to give up the precision of the grinding technology.
The development manages to adapt to manufacturers’ different runs with maximum quality thanks to the addition of a granite bed affording thermal stability and greater vibration damping.
The LT-400’s bed is a support free of residual stress which maintains its geometrical accuracy, making the work area much more stable than if it were made of another material. In addition, it is at an incline of 45 degrees to favour optimum stock removal.
The development likewise has cross slides equipped with contactless hydrostatic technology, ensuring zero wear in the guiding system, preventing the stick-slip effect and offering great damping capacity. The hydrostatic system ensures thermal stability through constant control of the oil temperature.
The linear motors of the X and Z axes are controlled by optical scales cooled to a controlled temperature. These motors significantly lengthen the maintenance intervals in comparison with other conventional systems for movement transmission because they lack intermediate mechanical elements.
Also of note is the head fitted with hydrostatic bearings and the integrated motor, both of which are cooled.
The machine is fitted with a mobile tailstock driven by a linear motor which helps speed up the process of setting up the change of the workpiece.
This lathe meets the requirements for manufacturing hydraulic pieces, bearings, spindle nuts and parts for equipment thanks to its capacity for machining high-hardness materials with precision to less than a micron.
3. Internal grinding for workpieces of great length
The EMO is also the place chosen by the company to exhibit its ILD-600 internal grinding machine, a completely new solution developed by its German subsidiary, DANOBAT-OVERBECK, for high-precision internal, external and face grinding on workpieces of great length with complex geometries.
It is a state-of-the-art solution for grinding spindle housings, axles, toolholders, bearings, hydraulic components and machine tool components, offering high-precision machining in workpieces of up to 1300 mm long -including the clamping system- with diameters of up to 760 mm.
This new development has a very long work table and a B0 axis allowing for the grinding of conical surfaces, as well as automated cylindrical corrections, without the need to mount a specifically sharpened wheel or resort to interpolation.
One of the main technical advantages of this development is that the wheel only moves along one axis, which is why the usual so-called “jagged edges” effect is avoided.
The new ILD-600 is characterised by a prolonged Z axis and a 3-position dressing turret. This new solution, to be launched at EMO, completes DANOBAT-OVERBECK’s offer of universal internal grinding machines for workpieces with bore of up to 400 mm deep.
The company’s entire ILD machine range, which carries a movable W axis for clamping large workpieces, was designed for holding a 4-spindle turret and an integrated measuring probe supported by control software. This probe enables continuous monitoring of the process without the need to remove and reclamp the piece, and also permits the detection of minimum modifications of the dimensions of the wheel, as well as the corresponding corrections in the CNC program without interruptions.
In short, the ILD-600 enables precision grinding of complex geometries with constant supervision of the process with no need for interruptions, a factor leading to increased efficiency.
4. A solution for non-cylindrical shapes and radii
The IRD-400 grinding solution offer which the company intends to take to the fair includes internal, external, surface and radius grinding, a solution especially designed for machining dies and moulds.
The main advantages offered by this development are the maximum precision results obtained for pieces with high geometric complexity and with high productivity.
The grinding machine achieves highly accurate finishes thanks to its B0 axis which swivels up to 91 degrees. Axis control means complex internal shapes can be made using one single wheel and in one contour line, thus maximising productivity.
With this model, the 4-spindle turret includes a measuring probe integrated in the software with which the starting position of the workpiece can be detected. This ensures that, on the final finishing run, the system reaches the required measurement with precision. In round contours, roundness deviations of 0.5 µm can be reached.
Another of the peculiarities of this development is the high degree of exact synchronisation of all the movements of the axes, including the rotation axis of the workpiece (C0), thus enabling eccentric grinding. This feature means that complex geometries can also be machined with the aid of coordinate grinding, and square, rectangular or freeform shapes can be made to great precision.
5. Vertical grinding of complex geometries, thoroughly conforming to clients’ requisites
As part of its offer of vertical grinding machines, DANOBAT will take its new model, the VG-800, to the EMO in Hannover. This model was designed for the grinding of medium-sized pieces (800 mm in diameter and 600 mm high) and with significant technical complexity.
The development, a result of a great effort in engineering, which can be appreciated in its compact design including independent slides for maximum precision in positioning, offers a high degree of customisability and can be adapted to meet the requirements of each client.
The VG-800 range has a turret enabling a large range of configurations which afford these machines the necessary versatility and flexibility to complete different machining processes in one set-up.
The development fully adjusts to the client’s machining needs due to its capacity to incorporate different technologies to carry out grinding, turning, drilling, boring and milling operations as well as measurement processes.
This new machine head is fitted with a high frequency spindle for internal grinding and a tangential spindle, both of which were developed by DANOBAT.
The VG-800 solution has a tool with a capacity to measure internal, external diameters, surfaces and cones, permitting intermediate measurements and offering flexible solutions for reaching high precision machining.
In addition, the C axis includes hydrostatic technology ensuring roundness to less than a micron and an optimum surface finish.
The linear motor of the X axis, controlled by optical scale, is cooled to a controlled temperature and affords the machine the necessary dynamic capacity to make high-precision interpolations.
This development comes with DANOBAT DoGrind software with a program library for grinding, turning and measuring as well as a module for energy savings and sustainability.
6. A horizontal development for large workpieces
DANOBAT is also to present its HG-72 horizontal grinding machine in Hannover. It can machine workpieces of up to 3,000 mm long, 740 mm in diameter and 1.5 tons in weight.
The main advantage of this solution lies in its capacity to meet all grinding needs in a flexible way and can be adapted to clients’ demands.
The machine is fitted with a three wheel head allowing for the machining of external, internal and curvic diameters. This spindle, which swivels on its own vertical axis and manages to reach all points on the workpiece, is driven by a 22-kW motor generating peripheral speeds of up to 60 m/s with wheels with a maximum diameter of 610 mm.
With these features, the machine can meet all grinding needs, including workpieces with Ra 0,1, in one set-up and guarantees geometric quality.
The machine is fitted with a DANOBAT MDM-400 multi-diameter measuring device which has, so far, only been available with the 300 and 500 models of this same range. The company has broadened its offer of this development and also has a wide selection of heads with an aim to adapting to the needs of each client.
The MDM-400 is capable of measuring diameters from 20 to 400 mm and works simultaneously with the machining process, a characteristic whose main advantage is the possibility to avoid the subsequent measuring process, and means that the grinding process is carried out in one operation.
DANOBAT’s MDM has a repeatability of ± 1.5 micron, it can measure diverse diameters and has the capacity to make post-process measurements once the grinding cycle has been completed and before the workpiece is removed.
7. High precision in slender pieces
The LG-1000 completes DANOBAT’s offer of grinding machines presented at EMO. The machine was developed for grinding slender workpieces requiring high precision with efficiency and productivity and guaranteeing the highest of quality standards.
The LG-1000, an ultra-precision grinding machine offering a high degree of customisation and guaranteeing very high machine availability, has a steady rest for monitoring which is CNC controlled and guarantees optimum cylindricity even in the most slender workpieces.
The LG family was developed for the manufacture of precision hydraulic parts, automotive parts, cutting pieces, cams or components with eccentric diameters.
In addition, it affords extraordinary repeatability, due to its natural granite bed, the linear motors and the added optical scales.
The wheelhead, fitted with cooled electro-spindles, reaches a maximum peripheral speed of 120 m/s covering the necessary range for grinding with conventional abrasives (45-60 m/s) or superabrasives (20 -120 m/s).
This development also comes with DANOBAT DoGrind software, an intuitive, user-friendly system which was developed by the company’s engineers.
- 4.0 technologies for the factories of the future
During the course of the fair, DANOBAT will likewise explain its focus on industrial digitalisation, which is structured around an offer of intelligent developments using 4.0 technologies, with an aim to forging ahead in the automation of real manufacturing environments.
“We have designed solutions allowing us to build intelligent plants with the capacity to work autonomously, thanks to the integration of information and communication technologies, enabling the capture and processing of data from the machinery. Not only do we have a deep understanding of technology but we also have consolidated experience in the manufacturing field”, says Xabier Alzaga, DANOBAT’s managing director.
By way of an example in this respect, the company has developed Smart HMI, an intuitive interface aiding the operator and facilitating the use of the machinery, thus raising productivity.
This development, which is installed in all the machines presented at the fair, allows quick and easy access to all the information on the status of the machine and its operation in a centralised fashion. Moreover, its design enhances usability and user experience.
Smart HMI helps optimise maintenance cycles as it shows the information relating to the status of the workpieces based on usage time, provides automatic notifications and maintenance instructions and improves reliability thanks to the self-diagnosis operations.
The development’s main functions include logical handling of control, documents on screen, assistance for identifying faults, monitoring of energy consumption, as well permitting the use of communication protocols.
The company has likewise developed a platform for capturing, storing and processing data called Data System which means the status of the machine can be monitored.
This development keeps the user informed of the situation and the working of the manufacturing process in real time, it lays down patterns, identifies tendencies, anticipates faults and implements intelligent maintenance strategies.
Last of all, DANOBAT has created an integral control system that coordinates and runs the operations of the equipment, machines and solutions in the same workshop or factory in a completely safe way and guarantees automated operation with maximum efficiency.
The solution, called Control System, enables the control, monitoring and supervision of data of all the stages of the machining process in high complexity manufacturing lines, made up of different machines and equipment.
- From technologically advanced machinery to high added value services
Apart from its history in the manufacture of innovative solutions incorporating cutting-edge technology, the company has a service offer aimed at delivering intelligent machine management, at incorporating technological advances to lengthen life cycle, at improving maintenance strategies and evolving and optimising production.
DANOBAT is characterised by the global management of all the projects it develops, which is why high added value service rendering is a key element that contributes to guaranteeing that the machines continue to work throughout their useful life like they do on the very first day.
To be precise, DANOBAT’s services, which are also to be presented at EMO in Hannover, are aimed at providing value to machines through the technological upgrading of the equipment and the incorporation of devices and functions that improve their operation.
Moreover, the company is also working on the development of strategies to help obtain maximum performance of the equipment and guarantee the quality of the pieces manufactured using advanced maintenance, the intelligent management of parts and a the creation of a broad network of experts wherever the machines are installed.
DANOBAT has predictive, preventive and corrective maintenance services for the purpose of raising the availability of the machines, enhancing their reliability, avoiding unnecessary downtime, improving performance and actually anticipating faults.
- With the Italian market in the spotlight
As part of its push for international expansion, the machine tool manufacturer aims to reinforce its presence in Italy.
The company has recently entered into a major alliance with Alberto Tacchella, a prominent expert in industrial manufacturing in the Italian market.
It is a partnership agreement with which DANOBAT seeks to intensify its stake in the transalpine country and strengthen its positioning in a highly competitive market where the Basque company is already working with major companies like Avio or the railway manufacturer Lucchini.
Born in the Italian region of Piamonte in 1960, and Doctor Honoris Causa in business management engineering and technology from the University of Oradea (Romania), Alberto Tacchella has spent his entire career working in the industrial manufacturing, production systems and machine tool sector.
The alliance entered into by both parties will allow DANOBAT to form closer links with their clients and promote the existing relations of trust.
“The partnership between DANOBAT and a person with such a track record in the grinding field as Alberto Tacchella will allow us to reinforce our presence in Italy, a strategic market for our company, and characterised by the high-quality standards required”, points out Xabier Alzaga, managing director of the cooperative.
As part of this strategy for intensifying DANOBAT’s presence in Italy, the company has likewise announced its physical presence with the setting up of 2.000 m2 of industrial premises in the municipality of Bistagno.
The plant, which will be used for commercial purposes and for rendering maintenance and post-sales services, is aimed at supporting DANOBAT’s activity in Italy and delivering a more hands-on service to the clients that the company has in the country.
About DANOBAT
The machine tool and production system manufacturer DANOBAT specialises in offering technologically advanced solutions and services which are fully adapted to clients’ needs for industrial manufacturing.
Belonging to the DANOBATGROUP and a member of the MONDRAGON Corporation, it is highly internationalised and designs high added value solutions.