Danobat showcases its latest solutions in high precision and production grinding at Mecspe
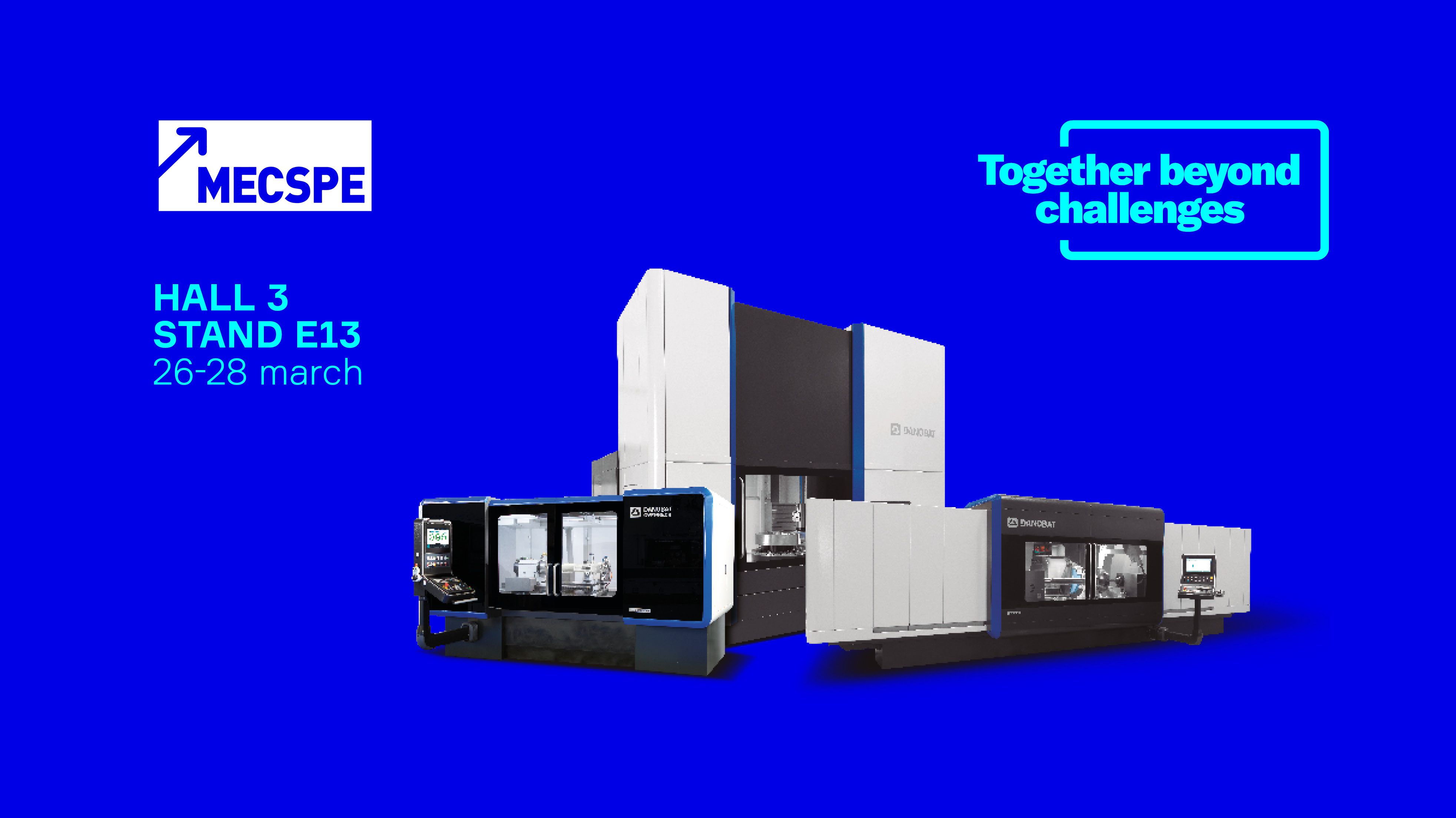
Danobat will be showing the latest technological solutions in Hall 3 stand E13 at Mecspe 2020, which will be held from March 26th to March 28th in Parma. Visitors will be able to see high precision and production grinding solutions.
In order to strengthen its presence in the Italian market, Danobat has a Centre of Excellence and a sales & service office. The Centre of Excellence is where Danobat’s solutions to customer challenges start taking shape. A place to see machines working, to test critical components and implement new developments. But most importantly, a place where Danobat’s customers can experience that they are taking the right decision with Danobat as a precision grinding and production partner.
The company will be exhibiting a Danobat CG machine for external grinding and the IRD-400, made at the German manufacturing plant Danobat-Overbeck, for internal and radius grinding operations.

DANOBAT-OVERBECK IRD-400S: A PRECISION GRINDING SOLUTION FOR A WIDE VARIETY OF MATERIALS
More and more customers are currently demanding shorter delivery times, a higher flexibility and universality in terms of applications, productivity and processes. That is why Danobat-Overbeck is offering the new IRD-400S machine model to the Italian market. The IRD-400 is designed for internal, external, face, non-round and radius grinding operations and can be applied for a wide variety of applications and materials. The machine comes with a predefined configuration to which customers can then add options and accessories. This guarantees an optimized price and delivery. All these aspects are brought to the Italian market through Danobat’s Excellence and Service Centre in Bistagno, where and IRD-400S is shown.

The main technical advantages offered by the IRD-400S are the precision results obtained for geometric complex workpieces, combined with a great productivity. The grinding machine achieves optimum surface quality finishes and low geometrical and dimension tolerances. All thanks to its B0 axis, which swivels up to 91 degrees. Moreover, axis control allows machining complex internal shapes using only one single wheel in one contour line. This greatly maximizes productivity.
The spindle turret in the IRD-400S includes a measuring probe which detects the starting position of the workpiece. This ensures that the machine reaches the required precision tolerances at the final machining operation. This machine offers roundness accuracies of < 0.5 micron.

DANOBAT CG-600: NON-STOP GRINDING WITH 98% ANNUAL AVAILABILITY
Great productivity under the most demanding conditions, low costs per part, an annual machine availability of 98%, short delivery times and durability are the most shared concerns of the manufacturing industry. The CG machine range has been developed in close cooperation with customers so that it meets all current market requirements.

CG-600 is designed for external operations and can be applied for a wide variety of applications. The grinding machine has a rigid structure, allowing it to successfully meet the customer’s high productivity demands. The wheel head, reaches a maximum peripheral speed of 80 m/s covering the necessary range for grinding with conventional abrasives. As a result, cycle time is considerably reduced, wheel life is increased and process stability is achieved. All CG machines come with the intuitive, in-house developed and user-friendly software Danobat DoGrind+.
Danobat also offers turnkey, automated solutions for the CG machines consisting of standard in-house developed modules. These compact, efficient and cost-effective solutions ensure a further boost in productivity. Apart from standard integrated automation solutions, external turnkey systems can also be provided in order to meet specific customer requirements.
The CG machine range is designed in such a way that a 24/7 production with only minimum service intervals is guaranteed. In addition, Danobat maintains a large stock of OEM parts. These are delivered quickly and directly without the intervention of secondary parties. All this contributes to the high annual machine availability of 98%.
