Danobatgroup presents its latest advanced manufacturing solutions for the machine tool sector at the BIEMH
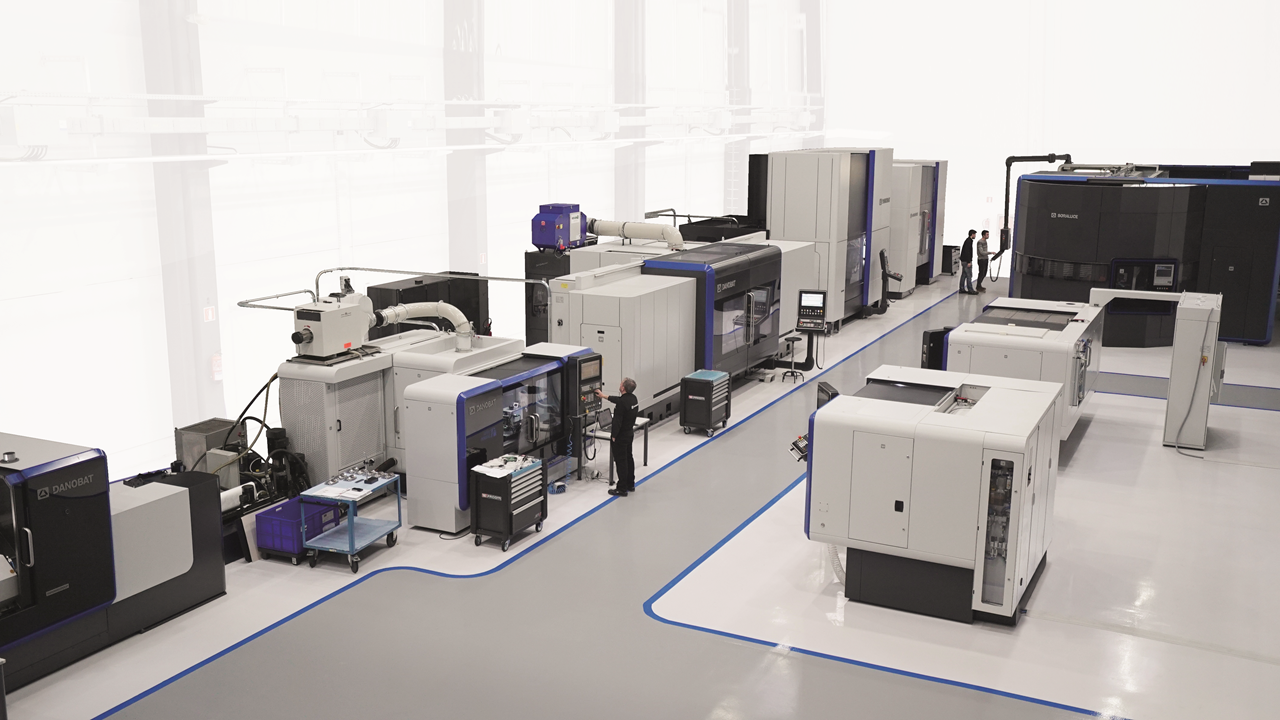
The business group Danobatgroup, specialising in the manufacture of machine tools and advanced production solutions, will again be present at the next International Machine Tool Biennial (BIEMH), which will take place from 13 to 17 June at the Bilbao Exhibition Centre (BEC) in Barakaldo, Bizkaia.
The Biennial has become a great opportunity for showing Danobatgroup´s extensive experience in the development of advanced solutions. These solutions have been specifically designed for the manufacture of high added value parts adapted to the needs of manufacturers in strategic sectors such as aeronautics, automotive, railway, capital goods and energy generation.
The exhibition space at stand C09 in hall 1 of the BEC, the group will hold the full potential of our leading brands, Danobat (and its subsidiaries, Hembrug and Overbeck) and SORALUCE, in the development of advanced machines, solutions and services of machine tools. These machine tools are equipped with the latest technologies in grinding, turning, milling and boring in order to ensure maximum precision and reliability in the different manufacturing processes, such as the automation of advanced machining processes and of robotised inspection systems for the handling of workpieces.
High precision solutions for machine tools
Danobat, one of the principal manufacturers of high precision grinding machines and lathes in Europe, focuses on the design, development and manufacture of machine tools and high-added value production systems, in order to offer its customers flexible solutions adapted to their needs, and with which parts can be manufactured with maximum precision and high productivity rates.
At the BIEMH, among other new products, DANOBAT will exhibit one of Hembrug’s most representative machines, the Mikroturn 100, an example of the cutting-edge technology that the Dutch brand offers in precision hard turning. “This is the Mikroturn® lathe which is aimed at a large variety of applications such as bearing rings and rollers, ball screw nuts, gears and shafts, hydraulic liners and pistons, as well as a wide variety of mould and die components”, said Oscar Hernández, head of Danobat´s sales department.
This machine, constructed on a fully hydrostatic natural granite base, can turn hardened and non-hardened workpieces of up to 450 mm diameter with high precision. Furthermore, it provides geometrical precision of 0.1 to 2 µm, with a surface roughness of Ra 0.1 to 0.4 µm, as well as dimensional precision of up to 2 µm on hardened steel (up to 70 Hrc). Furthermore, thanks to the lack of metal contact between the moving components, machining precision is maintained even after the machine has been used for decades.
Danobat, which has production plants and centres of excellence in Spain, Germany, United Kingdom, the Netherlands, Italy, the United States and China, will also be presenting its latest solutions developed by its German subsidiary, Overbeck, a brand with more than 90 years experience in the development and manufacture of internal, external, face and radii grinding machines.
60 years at the forefront of technology
For its part, Soraluce, which this year celebrated its 60th anniversary and its international leadership in milling, boring, multifunction and automation solutions, will exhibit some of its most innovative proposals to the public at the BIEMH, such as the travelling column milling machine, SORALUCE FLP, a solution that raises productivity to a higher level by providing maximum cutting capacity and flexibility.
The milling machine, which has multiple configurations, provides an energy consumption saving of more than 30%. Furthermore, the equipment, which guarantees high dynamics with speeds that reach up to 35,000 mm/min and facilitates pendulum machining with several work areas ensuring 0 downtimes.
Among other notable characteristics, the floor type milling machine, which incorporates a universal head with a positioning precision of a thousandth of an inch, has a longitudinal travel of 12,000 mm, vertical travel of 22,000 mm, and transverse travel of 1500 mm, which offers excellent versatility and a wide range of options for adapting to most productive requirements of its customers under the highest standards of efficiency, quality and precision.
The machine tool manufacturer is maintaining its commitment to technology by developing high added value services and offering expert advice to its customers. In this regard, as explained by David Gonzalez, the Soraluce sales director, during the Biennial “we will be presenting our smart damping solutions for raising stock removal capacity during machining, developed thanks to our high technical skill and knowledge of the engineering applied to manufacturing solutions.”
The attendees will have the chance to learn about these technologies at first hand through live demonstrations. Moreover, live tests will be carried out on its active smart damping system, DAS®, which monitors the machining process and selects the best alternative for eliminating vibration, as well as the active damping device DWS for eliminating chatter which is usually generated during the machining of flexible workpieces, thus increasing the cutting capacity of the equipment and raising the efficiency of the machining processes. The latter is being submitted for the BIEMH Innovation Prizes at this event.
“And, for us, commitment means always offering the best to our customers, ensuring maximum availability of use, above 95%, on our machines, in order to ensure the longest possible usage time of the equipment with less downtime, thus increasing performance and productivity of any project” stressed the Soraluce sales director.
Latest generation non-destructive testing
Within the Danobatgroup exhibition space, the latest developments from Endity will also be exhibited, a company that specialises in non-destructive inspection (NDT) solutions with high-added value workpieces. The company was created in 2020 by the industrial group and its research partner IDEKO as a response to the need of industrial companies to introduce non-destructive testing within their advanced manufacturing strategy.
Among other innovations, this non-destructive testing specialist company will present the E-Blade, a new completely stand-alone inspection system for wind turbine blades, in a real inspection environment within the stand itself. In this way, the attendees will have the chance to check in situ some of its most innovative characteristics, such as the level of autonomy and its capacity for digitalisation of the results.
Although this solution, based on ultrasound technology, is focused on the wind industry, Lander Sagarna, sales director at Endity explained “this is a good example of the level of sophistication that we can offer in other industrial sectors such as railway and other technologies such as induced currents”.
Commitment to people and talent
With the emergence of new technologies, the industrial manufacturing sector is experiencing significant changes that require new professional profiles which are capable of addressing the challenges posed by the digitalisation of production environments. In this scenario, promoting the bringing together of company reality in this area and the academic world has become a key factor for attracting new professional profiles.
For this reason, at the BIEMH, Danobatgroup will be strongly involved in the industrial employment fair WORKinnTalentHUB to strengthen its commitment to people and talent. During the job fair, the industrial group will share its value and business model proposal, which places professionals at the centre of its strategy. The event will also be used to collect CVs from the attendees and to make a first contact.
About Danobatgroup
With a track record of 65 years in the field of technologies applied to industrial manufacturing, Danobatgroup has a workforce made up of more than 1300 highly qualified people. The group is an international benchmark in the machine tool sector and technologies applied to industrial manufacturing.