Latest DANOBAT and SORALUCE machines to showcase at CIMT 2015in Beijing
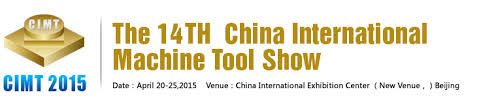
DANOBATGROUP will exhibit the latest developments and technologies of its two product brands, DANOBAT and SORALUCE, at the 14th China International Machine Tool Show -CIMT 2015-.
DANOBATGROUP will showcase in Hall E2, stand 201, the big dimension floor type milling-boring centre SORALUCE FXR-16000-W, the high precision DANOBAT-OVERBECK IRD 400 horizontal internal and radii grinding machine and the DANOBAT Underfloor wheel lathe for corrective maintenance of railway rolling surfaces and brake discs. On the stand a model of a full automatic railways axle, wheels, wheelset machining, assembly and inspection line will be also showcased as well as detailed information of other products such as lathes, grinding machines, milling boring machines, punchingand bending machines, laser cutting machines and turnkey solutions for oil&gas and railway industries.
DANOBATGROUP will exhibit the latest developments and technologies of its two product brands, DANOBAT and SORALUCE, at the 14th China International Machine Tool Show -CIMT 2015-.
DANOBATGROUP will showcase in Hall E2, stand 201, the big dimension floor type milling-boring centre SORALUCE FXR-16000-W, the high precision DANOBAT-OVERBECK IRD 400 horizontal internal and radii grinding machine and the DANOBAT Underfloor wheel lathe for corrective maintenance of railway rolling surfaces and brake discs. On the stand a model of a full automatic railways axle, wheels, wheelset machining, assembly and inspection line will be also showcased as well as detailed information of other products such as lathes, grinding machines, milling boring machines, punchingand bending machines, laser cutting machines and turnkey solutions for oil&gas and railway industries.
SORALUCE FXR 16000-W
The FXR-16000-W milling boring centre is a multi-purpose milling and boring machine. Its rigid and stable design provides the highest precision and productivity benefits when machining large components. The modular design of the machine offers remarkable versatility and can be equipped with a large range of optional accessories, enabling the machine to be adapted to customer’s needs with high efficiency and precision. It is the ideal solution for machining components belonging to sectors such as energy (wind-power, gas, nuclear), ship-building and capital goods.
The extremely heavy machine column with its “box in box” design together with the wide machine bed with 3 guideways allows for vertical traverses of up to 6500 mm and a ram cross traverse of up to 1900 mm. The heavy duty design in conjunction with the machines high dynamics offers the proven optimum in power and cutting speed capabilities, reaching up to 71 kW in S1 operation and 88kW in S6 operation and 2500 rpm.
Furthermore due to the travelling column concept of the machine, the machine can be equipped with several working stations, thus allowing for simultaneous machining and loading of different workpieces.
The machine incorporates several innovative technological developments such as the world’s first “DAS” Dynamic Active Stabilizer which eliminates vibrations produced during milling and and increases machining performance by up to 300%, whilst improving surface quality, providing constant efficiency independent of head position in the work area, reducing maintenance costs and increasing tool working life by up to 30%; the Modular quill spindle, a patented system, unique in the market that interchanges the quill spindle with the rest of the heads fully automatically, thus allowing to having different quill spindles with different diameters and lengths. Comparing to traditional quill solutions, the SORALUCE exclusive modular quill spindle allows the same distance between quill spindle and milling heads to be upheld, allowing 5-sided machining in the same set-up without any additional positioning of the workpiece at a long distance away from the machine; and the Ram Balance, a dynamic ram traverse movement compensation system (Ram Balance System). This system, which consists on an CNC controlled electromechanical system assembled within the vertical saddle, increases particularly the precision when the machine is equipped with the automatic head changing system, as it allows for accurate correction of the mechanical ram deviation irrespective of the different weights of individual milling heads.
DANOBAT-OVERBECK IRD-400
The DANOBAT-OVERBECK IRD-400 belongs to the three-model IRD range of high precision grinding machines for internal, external, radius, face and non-circular grinding. With a maximum internal grinding diameter of 200 mm, its workpiece swing diameter is 400 mm and maximum workpiece weight is between 70 and 170 kg.
The integrated B axis of the workhead, with a swivel range of +95º/-15º, is combined with 3-axis interpolative software to allow the grinding of different radii without manual re-setting of the pivot points. The T-slide configuration (400 mm X axis travel/400 mm Z axis travel) contributes to a compact machine design. Both slide elements are characterised by fast traverse speed, precise positioning and low maintenance requirements.
The direct driven workhead ensures the highest possible roundness quality, while contributing to flexibility and short change-over times. Up to 4 grinding spindles plus a measuring probe can be mounted on the wheelhead. Both high frequency and belt-driven spindles can be used. mm achieving a high stock removal and reducing the number of operations.
DANOBAT D2500 Underfloor wheel lathe
DANOBAT D2500 underfloor lathe is a machine tool specifically designed for corrective maintenance of railway rolling surfaces and brake discs, which does not require train axle dismantling. It is also designed to regenerate the wheel profiles subject to normal wear and deformation caused by the wheels travelling along the tracks. Underfloor wheel lathe includes all necessary measuring instruments enabling the rolling conditions that ensure the safety tread:
- Wheel geometry measurement device: Early detection of profile degradation, avoiding derailment and other risks resulting from improper rolling.
- Out-of-roundness testing device: Early detection of shooting jump, reducing vibration and noise.
Some benefits of the DANOBAT underfloor wheel lathe are:
- Low civil work requirements due to shallower pit
- Optimum bogie clamping
- Improved safety by integration with shunting car
- 70%reduction of operational costs: The inspection based on automatic systems, reduces drastically maintenance costs. If the evolution of the parameters is checked, abnormal wear and tear can be detected and remedied.
- 25% wheelset life increase: The efficient turning using economic or intermediate profiles increases notably the life of the wheel without affecting the safety.
DANOBAT D2500 also integrates intelligent maintenance software that transforms system data from the machine to the maintainer. Data is converted to information, by adding syntax and presenting it in an understandable form.