Intelligent solutions and multitasking machining, SORALUCE’s proposal at the BIEMH Fair
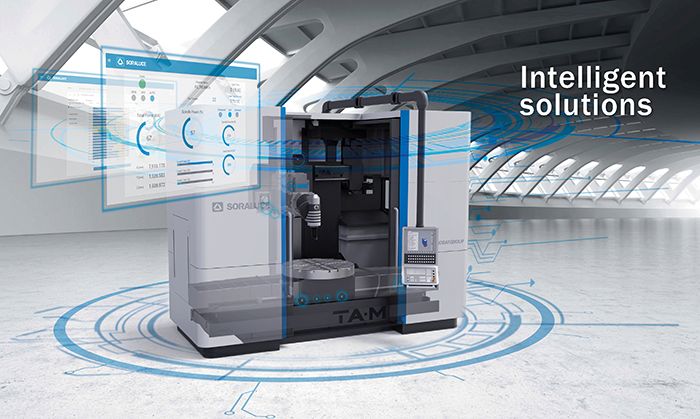
-
SORALUCE presents multitasking solutions capable of performing milling, turning and grinding operations in a single set-up, thus helping to maximise productivity.
-
SORALUCE advanced technology with live demonstrations of SORALUCE DAS+, which maximises machine cutting capacity, and SORALUCE VSET, which reduces calculation times for fitting and alignment of large-sized blanks.
-
SORALUCE is to stage a live demonstration of its SORALUCE Digital platform, a high value-added platform for increasing the availability and productivity of its solutions.
-
SORALUCE integrates smart sensors into its machines so as to offer advanced maintenance services.
At SORALUCE we see innovation as a process that begins and ends with the customer: it begins with the identification of their needs and ends when the market acknowledges the technological innovation of our products and places its trust in us.
Based on in-depth research, experience and the requirements of its customers, SORALUCE develops innovative technologies systematically exceeding the existing limits in milling, boring and turning. The new developed solutions to be showcased in BIEMH 2018 provide customers with a decisive competitive advantage. Intelligent solutions using innovative technologies intended to optimise the production processes of our customers.
Our commitment to technology involves increasing cutting capacity, increasing precision, digitising products and processes and servitisation.
New technologies such as VSET and DAS+ enable firms to replace the experience and expertise of their senior employees by smart functions incorporated into machines, resulting in higher cutting capacities and shorter machining times, thus ensuring maximum efficiency and the best possible performance.
A connected life can be fascinatingly easy. SORALUCE will demonstrate in Bilbao its digital ecosystem. Sensors and control information provide data as the basis for intelligent evaluations and optimizations. SORALUCE DIGITAL offers a complete and practice-oriented digital world.
Multitasking machines will be presented by the company as the solution for the future, providing maximum versatility, productivity and precision for production. Milling, turning, grinding and boring on a single machine, so that set-up times become spindle running times.
New SORALUCE TA-M, high performance capacity in milling, turning and grinding in a single machine
SORALUCE presents the new TA-M turning-milling centre, a multitasking solution aimed at maximising productivity. With the ability to perform milling, turning and grinding operations on the same machine, it offers large capacity and a wide range of machining functions for multiple types of workpieces of different sizes and shapes, with great efficiency and precision.
This model was designed to respond to the machining needs of various high demand components. The machine responds to multi-tasking and versatility requirements, maximising productivity and minimising the time to prepare a part. In this regard, the new SORALUCE TA-M multifunctional fixed bed reduces the number of clamps required, minimising both cycle times and potential errors.
The ability to carry out different machining processes efficiently and accurately, including turning, milling, grinding, boring, drilling and threading, are part of its identifying features.
SORALUCE provides a complete series of multi-functional capabilities thanks to the design of its turning heads, tables and customised cycles and a wide range of multi-function heads developed for multiple operations, for increased capability and functionality.
The machine is equipped with a table for milling and turning in two variants of Ø 1000 or Ø 1250 mm and a new SORALUCE H200T multitasking head for turning, milling and grinding operations. The H200T head is equipped with an innovative rotational locking system for the chuck, making it possible to use both milling and turning tools directly without the need for intermediate elements. In addition, the machine can execute grinding operations incorporating specific cycles to easy programming of the different operations, and integrate the necessary equipment for the dressing operation and the manual balancing of the wheel. The machine can be also equipped with specific coolant and filtering systems to guarantee an optimum workpiece surface finishing.
The machine has 1,250 mm of travel vertically and 1,200 mm across and has a capacity for parts of up to 8,000 kg for milling and 2,000 kg for turning in a range of speeds of 6 ÷ 400 rpm.
Designed to provide maximum stability, its high level of head torque power (28 kW / 479 Nm) and turning table spindle power (79 kW) makes it possible to carry out roughing operations with a great depth of cut. The structural elements are made entirely of cast iron, a material appreciated for its good intrinsic qualities in terms of stability and internal damping capacity.
Being compact and ergonomic, it stands out for its accessibility to the work area, with access from the front and rear to facilitate the set-up of parts and measuring operations, as well as monitoring the operation of the machine.
The new SORALUCE TA-M completes the wide range of SORALUCE multifunctional machines for workpieces with dimensions from Ø 1,000 to Ø 8,000 mm; highly configurable mobile column multifunctional centres (F range) with milling and turning tables and multifunctional gantry milling machines (P range).
Intelligent solutions
SORALUCE Advanced Technology:
SORALUCE offers users all the technology developed by the firm for increasing precision and productivity, such as Chip Breaker, Adaptive Control, Accura Heads and its revolutionary, successful DAS+ System, an upgrade of the current DAS® system, which includes more functions to increase the machining capabilities of our machines.
DAS+ includes vibration level monitoring, detection of chatter as well as two different extra strategies to suppress chatter: the new spindle speed tuning and spindle speed variation functions. This new function monitors the machining process and runs an internal algorithm that looks for the best cutting conditions to increase the stability of a particular operation. In the event of instability, the algorithm considers the chatter and excitation frequency generated by the tool and selects the best strategy to overcome the problem, automatically activating the DAS+ system, selecting the optimal spindle speed where chatter is suppressed or introducing a continuous harmonic oscillation in the spindle during the machining process. The machine becomes an assistant for the operator which can concentrate on maximising the use of the machine’s capabilities.
DAS+ makes the machine more intelligent and increases the productivity and robustness of the process, achieving reduced cycle times, longer tool life, a significant improvement of the surface quality and reduced machine wear. It includes all the knowledge and experience of SORALUCE in the field of machining dynamics, for the benefit of our customers.
In the field of large workpieces, SORALUCE is to present its new SORALUCE VSET measuring system based on 3D vision technology, which reduces the time required to calculate the best fit and alignment of large-sized blanks.
The system is based on photogrammetric technology, which measures workpieces from different reference points on the workpiece itself. The data generated during the measuring process is compared automatically with the 3D model of the workpiece to calculate the best fit. Once the blank workpiece has been checked it can be aligned on the machine using the same reference points.
This reduces the time spent on aligning and fitting blanks by as much as 70% and provides a 100% quality guarantee for worpieces from previous processes such as casting, forging and welding.
SORALUCE Digital:
The new digital paradigm in manufacturing makes the interaction between machines, people and processes easier. SORALUCE helps its customers to become more competitive by innovating in the field of industrial digitalisation, improving operational efficiency by connecting the machines to the cloud in order to enable a seamless production information flow and maximise the machines’ performance. The interconnection of the equipment and the possibility of obtaining and analysing data from machines, open up the path towards creating smart manufacturing environments.
In this context, SORALUCE presents the SORALUCE Data System, a machine data-driven analytics tool that extracts valuable insights from the machine-generated data and that monitors its status and condition to ensure that the running performance of the machining process is as high as possible. SORALUCE Data System is a powerful tool to maximise uptime and manufacturing efficiency.
SORALUCE Data System includes several features; among them, the display of the machine status in real time providing relevant information about the situation of the machining in progress. The tool generates reports regarding sensitive issues for the user such as production or process, energy consumption or the performance of the machining cycles. It helps to optimise the machining process variables through the diagnosis of key warning signs related to the maintenance of the equipment and thus increases the machine’s productivity and avoids unnecessary consumption. It also sends emails automatically in the event of a shutdown
Using specific hardware and applying the latest Big Data and Cloud Computing technologies, SORALUCE Data System collects and stores significant data from the CNC, PLC and sensors built into the machine and turns them into useful information. SORALUCE Data System brings together a set of services based on machine monitoring and Big Data to analyse the machining process and machine behaviour. It enables users to connect to the system remotely and securely via mobile devices including laptops, smartphones and tablets, and to have access to all the relevant information of the machines, factory logistics systems or other machines in the production system taking customers to the realm of the smart factory. In addition, it allows the connection with other machines of the factory and also with different management software applications such as ERP, MES, GMAO, etc.
Advanced monitoring via sensor technology:
SORALUCE moves in the era of digitalization towards more reliable machines, incorporating sensors that allow analysing the evolution of various signals associated with the state of the most critical components. The objective is to detect possible failures those components and avoid unplanned stoppages.
In this sense, the TA-M machine incorporates the latest developments in the field of sensorisation applied to machine tools. The sensorised elements are several, standing out the head, ballscrews and linear guiding systems. It allows access to relevant data related to the health of these components such as temperature or vibration.
The systematic recording of these signals in the SORALUCE Data System allows analysing the evolution over time and taking actions in advance from anywhere and at any time. The result is a precise diagnosis to reduce the impact derived from maintenance actions on production.
SORALUCE, Setting new standards
SORALUCE is the worldwide milling, boring and turning technology leader. Throughout its 55 years of history it has continuously made innovative and pioneering contributions in engineering that have become industry standards. Customers recognise SORALUCE for its expertise in milling, boring and turning solutions, always geared towards improving the customer’s efficiency and productivity, and for its technological capacity to customise each product based in the customer’s individual needs, likewise generating turn-key projects, designing and setting up complete lines according to the quality, efficiency and cost parameters required by the investor.
The European brand has extensive experience with over 2,500 machines sold, nearly half of them in Germany, a highly demanding market. It has also been determined that over the years, 80 per cent of customers have trusted in its products again.
SORALUCE is part of DANOBATGROUP, machine-tool division of MONDRAGON Corporation, one of the most important holdings in Europe. It has nine top-level manufacturing plants in Spain, Germany, the UK and the United States, an Excellence Centre in Germany, BIMATEC SORALUCE, and its own R+D centre with 120 engineers and 29PhDs and more than 30 years of history. DANOBATGROUP provides one of the most complete and solid multi-technological offers on the market. In 2016 it achieved a turnover of 260 million euros with a workforce of 1300, enabling it to continue with a high investment in R&D&i, amounting to approximately 8 % of its turnover.