SORALUCE SUMMIT | Portal series 2019
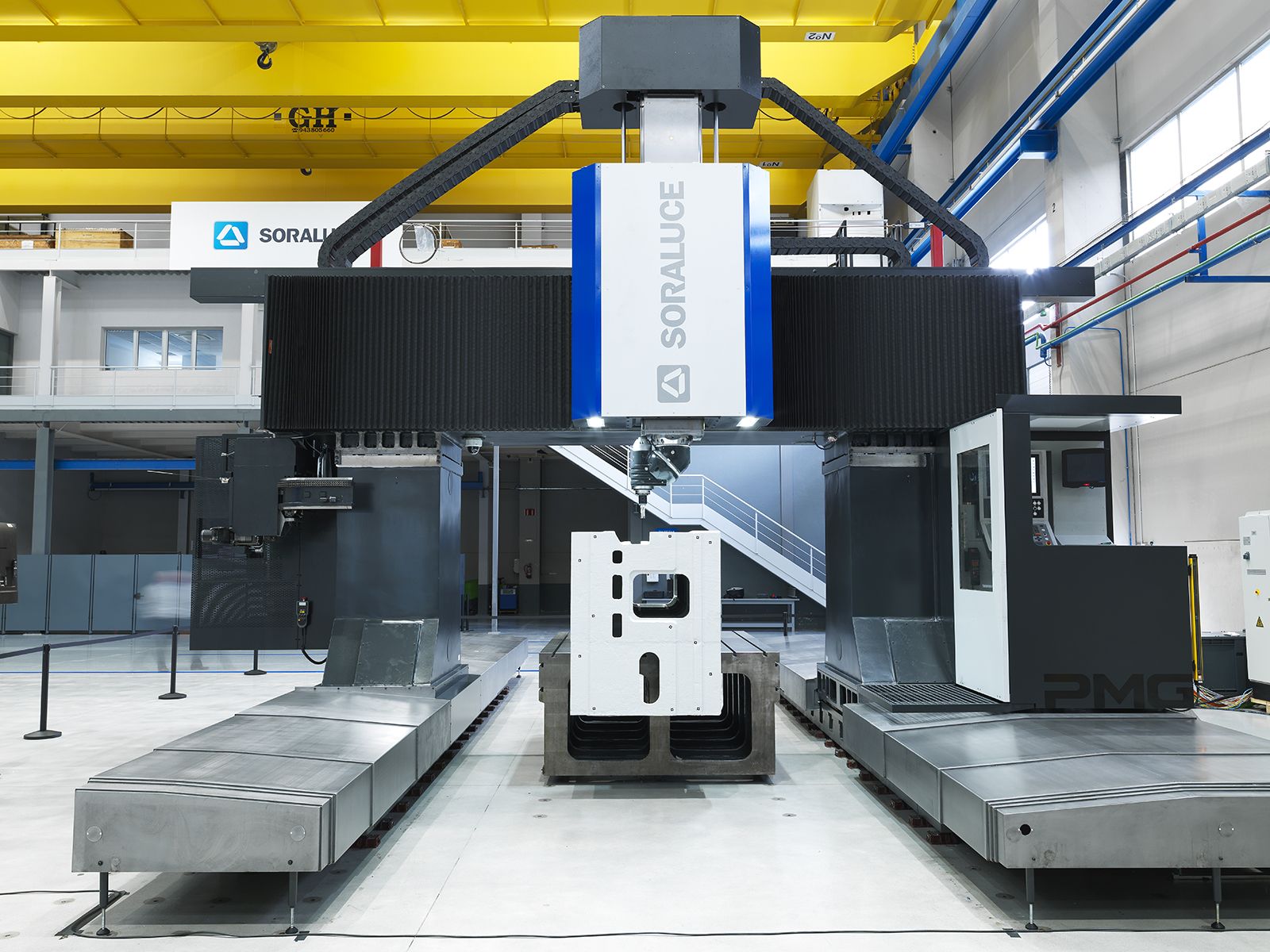
SORALUCE SUMMIT has been the opportunity for the sector’s professionals to discover the latest SORALUCE technologies and developments, which has been held from 20 to 22 March at the new PORTAL FACTORY, the most comprehensive and advanced manufacturing centre for large-scale, high power portal machines.
A unique chance to experience our capacities, in real machining conditions, and showcased by top specialists in milling, vertical turning and grinding. At the SORALUCE SUMMIT 2019 | PORTAL SERIES, SORALUCE has presented the benefits of the new solutions and technologies related to the new generation of SORALUCE portal machines.
World premiere SORALUCE Portal Series
The linchpin of the SORALUCE SUMMIT | PORTAL SERIES was the global unveiling of the extraordinary advantages of this new SORALUCE range for machining large components, as the brand yet again shows its leadership and its technological capability.
The new PORTAL SERIES unveiled is part of SORALUCE’s business development. Endorsed by its knowledge and experience in milling and turning technology as well as its position as technological leader in the sector, SORALUCE showcases a complete range of portal machines, including mobile table milling machines, gantry milling machines, multitasking machines, with fixed and moving cross beams, with a full range of heads and other options.
The new Portal Factory
SORALUCE also presented the NEW PORTAL FACTORY, the most comprehensive and advanced manufacturing centre for large-scale, heavy duty portal machines, which was also the venue of the Summit on this occasion. The NEW FACTORY PORTAL is a very important step forward in the development of the PORTAL SERIES, thus offering a response to the growing demand for machining large parts. The facility is exclusively focused on this type of machines, which account for all the production activity, along with the research and development projects for the portal series.
The new plant has meant an investment of € 9 million. It has a usable surface area of 4,900 m2 (140 metres long and 35 metres wide and 17 m high), which allows the manufacturing of large-scale portal machines. Its crane capacity is up to 80 Tn.
The new PORTAL FACTORY opened during the SORALUCE SUMMIT | PORTAL SERIES is a milestone in SORALUCE’s Strategic Plan 2017-2020 focusing on the expansion of the product range, technological differentiation, the development of customer sectors and the consolidation of SORALUCE’s presence on the new international markets.
Engineering power knowledge
Our aim is to create value for customers. However, it is not enough to meet expectations to be successful and we have to exceed them, which means designing and constructing new products, offering “best in class” services, being capable of customising our solutions and technologically leading the market. Furthermore, this package contributes to improve the productivity and cost-effectiveness of each of our customers. Therefore, the SORALUCE SUMMIT was the ideal setting to share experiences among professionals of the sector and build the future together.
A good example of this was special integral projects showcased by SORALUCE, specifically developed for some customers working closely on R&D&I and with the support of its research centre.
Multitasking solutions to increase the productivity and precision of machining processes
The multitasking solutions, which allow different machining operations to be integrated into one single machine, make it possible to reduce cycle times, save on costs and increase the efficiency of the machining processes.
In this sense, the European manufacturer of machine tools SORALUCE has reshaped the concept of “multitasking”, traditionally associated with the integration of turning and milling in one machine, thanks to the development of advanced technologies which allow the addition of grinding. This last operation is the phase which requires the highest level of precision during the machining process and the one which concludes the manufacturing of high added value industrial components.
“The technologies that we have developed at SORALUCE make it possible for the different stages of the machining process of components to be carried out using the same machine, efficiently, and providing high-precision results”, guarantees Andres Mazkiaran, Multitasking Product Manager at SORALUCE.
The multitasking concept developed by the company, which can be incorporated into the entire range of the manufacturer’s machines, provides high impact advantages such as cutting the amount of time dedicated to the loading, unloading and centring of parts as, given that the different tasks are carried out in one machine, these operations need only be completed once.
But, in addition to this, choosing a multitasking system implies a reduction in investment in terms of the number of equipment, a decrease in the amount of space needed in the plant itself as well as the amount of resources required.
Therefore, the multitasking systems are versatile, compact, provide great flexibility, increase efficiency in the process and make it possible to produce small batches efficiently.
The SORALUCE multitasking centres are equipped with mechanical transmission and high-torque multitasking indexing heads and SORALUCE tables which provide a high level of versatility as they make it possible to machine parts of different sizes and shapes.
With extensive experience in the field of milling and turning, SORALUCE develops customised cycles to complement the systems of manufacturers of numeric controls (CNC), such as the kinematic management of the heads which, using one tool corrector in the whole area, facilitates the programming of simple geometries and makes it possible to move from one process to another in the multasting solutions or customised cycles for different milling, turning and grinding processes. The SORALUCE SUMMIT | PORTAL SERIES allowed to assess in real situations the capabilities and advantages of these interesting options.
Applied technology:
As was to be expected, the applied technology was one of the featured aspects during the Summit and SORALUCE yet again showcased its application ability to provide major solutions to common problems in machining.
Smart damping solutions to boost stock removal capacity during machining
Machine tool productivity is often associated with material removal capacity. A number of parameters, some relating to the machine itself, such as its power output and dynamics, and other process-related criteria such as the tools, the material to be machined and the part itself determine the removal rate that may be obtained. However, it is normal to come up against problems concerning vibration. This can limit the predefined machining conditions, and lead to noise problems, poor finishing or even tool breakage. Elimination of chatter is a challenge for any operator.
This challenge has obtained a positive response from SORALUCE, which has developed a number of solutions to eliminate self-excited vibrations or chatter, boosting machines´ cutting capacity and improving the efficiency of machining processes. This is a field in which the company has been working successfully for several years and in which it has been recognized with prestigious awards.
Specifically, the team of dynamic behaviour experts at SORALUCE and its technology centre IK4-IDEKO has developed the Dynamic Workpiece Stabiliser (DWS), which was also part of the demonstrations during the SORALUCE SUMMIT | PORTAL SERIES. This system eliminates the chatter which usually occurs when flexible parts are being machined. DWS, patented, is an active damping device which consists of a controller and one or more inertial actuators placed over the part to be machined.
“One of its main benefits is a better surface finishing in areas where the part is more flexible, and the chance to boost productivity thanks to in-depth passes with no vibration problems. Its user-friendliness, adaptability to various parts and its portability are some of the other advantages of the device”, says Xabier Mendizabal, Head of R+D at SORALUCE.
DWS, a pioneer development on the market, provides an effective solution for the problems associated with machining slim-format parts. It is an improvement on traditional alternatives such as the design of costly special tooling, or less reliable and less effective solutions.
Another in-house SORALUCE development is the DAS+, a smart system which oversees the machining process and selects the best technological alternative to eliminate any chatter that may arise.
DAS+ has a user interface to control realisation of the process and avails itself of several strategies to eliminate chatter such as active damping of the ram, spindle speed tuning by automatic selection of optimum speed, and harmonic oscillation of spindle speed.
The solution, now available for new machines, can be fitted on request to machinery already operational. The system can boost productivity by up to 300%, with 100% cutting capacity through the complete workpiece volume. Besides, DAS+ also improves the surface quality of the parts produced, extends tool life, makes processes sturdier and reduces wear of the machine´s internal components.
In addition to DWS or DAS+ products, SORALUCE offers customised advisory services aimed at improving the stability of the machining processes. It consists of the study of existing machining methods and strategies, an analysis to determinate the origin of the vibrations and the approach of solutions to deal with chatter problems that may appear during machining.
Advanced vision system for the alignment of large parts
The machining of large raw parts requires a machine tuning procedure which is both lengthy and highly difficult, calling for the use of complex technologies which make the manufacturing process more expensive and lengthen equipment downtimes.
This preparatory phase for parts, which occasionally takes more time than the machining itself, implies measuring and calculating the fit of the part in order to confirm that it includes enough surplus material along all of the surfaces which are to be machined and, subsequently, to guarantee that it will be possible to achieve the end result. After these two stages, a third operation takes place which involves the alignment of the part in the machine.
With the aim of optimising this very process, SORALUCE has showcased during the Summit the advantages of its VSET system, based on 3D photogrammetry vision technology which, by means of its VSET Measuring and VSET Fitting modules, guarantees that the measuring and fitting phases are completed in a fast and safe way. These two stages are executed outside the machine, increasing machine availability and productivity thanks to transferring set-up times in measurements, adjustments and corrections to an environment outside the machine.
In order to carry out the whole process with the greatest agility possible, the company has developed and incorporated a third module into this solution which constitutes an alignment system, allowing the machining of raw parts to be perfected, meeting speed, ease and precision parameters.
This third model, called VSET ALIGNMENT, complements the processes carried out by VSET Measuring and VSET Fitting, as it allows the measurement and fitting results obtained during these stages to be automatically included in the numerical control of the machining centre itself in order to subsequently proceed with alignment in the equipment, reducing with the new software up to 70% the overall time spent in the whole process.
The VSET system process begins with the calculation of the surplus material in order to define the optimum alignment of the raw part. The VSET Measuring module uses photogrammetric technology to measure the part using several optical reference points or markers located in different areas surrounding it. Once this process is complete, the Fitting system automatically compares the information obtained with the final geometry of the 3D model of the part in order to carry out an optimum calculation of the local reference points. The report generated by this second model is sent to the machine so that the new VSET Alignment, installed in the controller of the machine itself, can implement an alignment of the part in accordance with the predetermined coordinate system.
The incorporation of this new module offers an effective solution in order to reduce the time spent on the aligning, fitting and measuring processes of raw parts and increases machine availability given that measuring and fitting are completed by external modules. The modular VSET system ensures the quality of parts from previous processes such as casting, shaping and welding; it increases the machine’s productivity and standardises machine alignment procedures without the need for specialised profiles.
Ultimately, the VSET system by SORALUCE is the solution for optimising preparations prior to machining processes and puts SORALUCE at the cutting-edge of industrial innovation.
Smart HMI: intuitive, ergonomic and easy-to-use intelligent interface, which shortens work times and increases the efficiency of the whole process
New functions that increase the efficiency of manufacturing processes, improved ergonomics and greater ease of use are some of the advantages offered by the new intelligent interface developed by the machine tool manufacturer SORALUCE. This flexible working environment adapts to the user’s needs and means operation times can be reduced.
The interface, called SORALUCE Smart HMI, is presented on a 24-inch wide-format touch screen. The solution is based on a new display which is compatible with the Heidenhain TNC 640 control. The system allows additional information to be displayed in an area of the screen adjacent to the control panel, increasing the information available to the operator. The display of this adjacent area can be alternated with the full screen option, allowing a more detailed display.
In this new display area, SORALUCE has incorporated different applications aimed at making the machine operator’s task easier by having new functions accessible from a single working environment. These include applications for the display of plans, documentation relating to the machining process, calculation of working conditions, access to user manuals or display of the work area through fixed cameras operated by users themselves, all visible in parallel with the program in execution.
“The main advantage of this development is that users can see the operations the machine is performing at the same time and in the same environment in which they consult, for example, 3D plan viewers, alarm management or the level of energy consumption”, says the specialist Jesús Álvarez, Head of the SORALUCE Digital Platform.
Thanks to this device - which is more intuitive, ergonomic and easy to use - job times are reduced, and the efficiency of the overall process is increased.
One of the most notable applications that SORALUCE has incorporated into its Smart HMI is the function of editing programs simultaneously with the manufacturing process. This application means that it is possible to execute a manufacturing program in the control area at the same time as editing another program in the new enlarged section. “Until now, the screen for editing programs alternated with the screen for displaying the process being executed. It was not possible to view both screens simultaneously, which restricted functionality for the user. This new feature provides users with a very significant benefit as it brings more agility and efficiency to the processes”, adds Álvarez.
The new interface - together with SORALUCE’s Data System platform, an analysis tool that extracts valuable information from the data generated by the machine and monitors its status to ensure the best possible performance of the machining processes - displays information in the user’s work environment regarding alarm management, machine usage, energy consumption or machine maintenance.
Within the Smart HMI, SORALUCE has also incorporated applications which it has developed itself. These include Indexmill software for calculating the work plane, useful for generating the machining program. Also included in the interface is the Interpolation post-processor, exclusive to SORALUCE, which calculates and generates the chuck trajectory interpolation program for multiple surfaces. Another of the applications offered is VSET which focuses on the alignment of parts being machined.
The new HMI also offers access to an external PC connected through Remote Desktop where, in addition to the applications offered, users can customise direct access to their applications.
SORALUCE has also developed new functionality on Heidenhain’s own CNC screen, using programmable keys such as custom diagnostic masks and help graphics for manufacturing cycles.
“These utilities have been designed to simplify the most frequent operations, recover procedures after machine interruptions, facilitate diagnostic functions through customised masks and improve ergonomics”, adds the expert.
About SORALUCE
SORALUCE is the global leader in milling, boring and turning technology. Since its creation 55 years ago, it has continuously made innovative and pioneering contributions to engineering that have become industry standards. SORALUCE is recognised for its expertise in milling, boring and turning solutions and has the ongoing aim of improving customers’ efficiency and productivity. The company is also noted for its technical ability to customise each product based on the customer’s individual needs, and to implement turn-key projects, designing and setting up full lines according to the customer’s quality, efficiency and cost parameters.
SORALUCE is a European brand which has extensive experience and a strong track-record, with over 3,000 machines sold (nearly half in the highly-demanding German market) and a customer retention rate of 80%.
SORALUCE is part of the DANOBATGROUP, the machine-tool division of MONDRAGON Corporation, one of the largest holdings in Europe. It has nine state-of-the-art manufacturing plants in Spain, Germany, the UK and the USA, an Excellence Centre in Germany (BIMATEC SORALUCE) and its own R&D centre with 120 engineers, 24 PhDs and more than 30 years of history. The DANOBATGROUP develops and supplies an extensive range of machine tools, turnkey lines and solutions for specific applications aimed at high-technology sectors and at customers with high technical requirements. In 2017, it achieved a turnover of 240 million Euros with a workforce of 1300, enabling it to continue making significant investments in R&D, which represent approximately 8% of turnover.