DANOBAT presents its latest developments at GRINDTEC exhibition
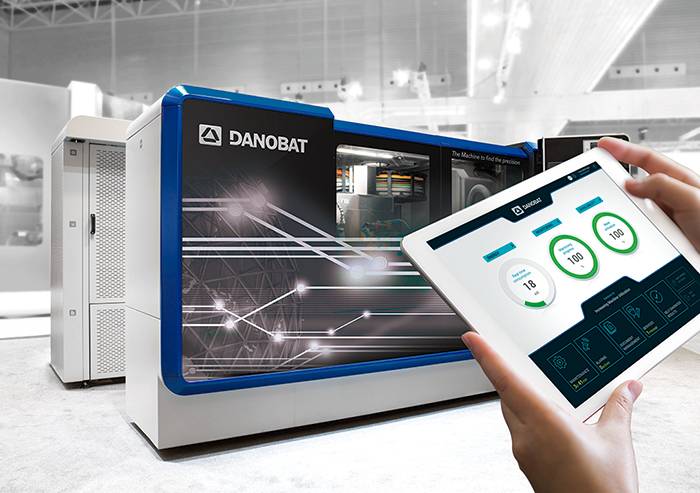
DANOBAT will be exhibiting at GRINDTEC which will be held at Ausgburg (Germany) from 14th to 17th of March.
The company will be presenting technologically advanced grinding machines as well as a hard turning lathe that achieves grinding precisions.
In addition, the company will avail of this opportunity to share its digital value proposition, composed of in-house technological developments based on industry 4.0 concepts with an aim to advancing in the creation of intelligent manufacturing spaces, fitted with interconnected equipment and capable of autonomous operation.
Below are the technologically advanced developments that DANOBAT is to present at the coming edition of the fair:
1. Maximum rigidity centreless grinding
DANOBAT will present the ESTARTA-650 centreless grinding machine, a solution characterised by being one of the most rigid grinding machines of these characteristics on the market.
The ESTARTA-650 was designed to meet current high-speed manufacturing demands for the purpose of significantly improving the cycle times and maximising production.
The main advantages of this solution are its high precision, a 30% rise in productivity and great rigidity.
This development can achieve 120 metres per second in throughfeed minimising the generation of vibrations. This characteristic -working at great speeds with maximum vibration absorption- is a key feature for successfully carrying out highly demanding grinding processes.
The grinding machine is fitted with linear motors, a granite bed, a drive head fitted with an additional support that does away with the cantilever, and a novel damping system.
The solution also has a rolling guide system, affording it greater sensitivity in movement. This last feature implies the elimination of the hydraulic component, making the ESTARTA-650 an environment-friendly sustainable grinding machine, requiring less consumption and maintenance.
2. LT-400: Grinding quality with turning flexibility
DANOBAT has years of experience on grinding and turning, with a combined knowledge of these two tecnologies, the LT-400 was developed.
High-precision turning machine for hard turning and with grinding capability, a development that is characterised by achieving maximum quality results with great flexibility and adaptability to the client’s needs.
The LT-400 adjusts perfectly to the demands of short-run manufacturers, who are required to frequently modify the type of parts they manufacture, but who request the precision of the grinding technology.
The development manages to adapt to manufacturers’ different runs with maximum quality thanks to the addition of a granite bed affording thermal stability and greater vibration damping.
The development likewise has cross slides equipped with contactless hydrostatic technology, ensuring zero wear in the guiding system, preventing the stick-slip effect and offering great damping capacity. The hydrostatic system ensures thermal stability through constant control of the oil temperature.
The linear motors of the X and Z axes are controlled by optical scales cooled to a controlled temperature. These motors significantly lengthen the maintenance intervals.
Also of note is the head fitted with hydrostatic bearings and the integrated motor, both of which are cooled.
The machine is fitted with a mobile tailstock driven by a linear motor which helps speed up the process of setting up the change of the workpiece.
This lathe meets the requirements for manufacturing hydraulic pieces, bearings, spindle nuts and parts for equipment thanks to its capacity for machining high-hardness materials with precision to less than a micron.
3. A solution for non-cylindrical shapes and radii
The IRD-400 grinding solution offer which the company intends to take to the fair includes internal, external, surface and radius grinding, a solution especially designed for machining dies and moulds.
The main advantages offered by this development are the maximum precision results obtained for pieces with high geometric complexity and with high productivity.
The grinding machine achieves highly accurate finishes thanks to its B0 axis which swivels up to 91 degrees. Axis control means complex internal shapes can be made using one single wheel and in one contour line, thus maximising productivity.
With this model, the 4-spindle turret includes a measuring probe integrated in the software with which the starting position of the workpiece can be detected. This ensures that, on the final finishing run, the system reaches the required measurement with precision. In round contours, roundness deviations of 0.5 µm can be reached.
Another of the peculiarities of this development is the high degree of exact synchronisation of all the movements of the axes, including the rotation axis of the workpiece (C0), thus enabling eccentric grinding. This feature means that complex geometries can also be machined with the aid of coordinate grinding, and square, rectangular or freeform shapes can be made to great precision.
4. Vertical grinding of complex geometries, thoroughly conforming to clients’ requisites
As part of its offer of vertical grinding machines, DANOBAT will take the VG-800 to the GRINDTEC.
The development, a result of a great effort in engineering, which can be appreciated in its compact design including independent slides for maximum precision in positioning, offers a high degree of customisability and can be adapted to meet the requirements of each client.
The VG-800 range has a turret enabling a large range of configurations which afford these machines the necessary versatility and flexibility to complete different machining processes in one set-up.
The development fully adjusts to the client’s machining needs due to its capacity to incorporate different technologies to carry out grinding, turning, drilling, boring and milling operations as well as measurement processes.
This new machine head is fitted with a high frequency spindle for internal grinding and a tangential spindle, both of which were developed by DANOBAT.
The VG-800 solution has a tool with a capacity to measure internal, external diameters, surfaces and cones, permitting intermediate measurements and offering flexible solutions for reaching high precision machining.
In addition, the C axis includes hydrostatic technology ensuring roundness to less than a micron and an optimum surface finish.
This development comes with DANOB
AT DoGrind software with a program library for grinding, turning and measuring as well as a module for energy savings and sustainability.
- 4.0 technologies for the automation of real manufacturing environments
During the course of the fair, DANOBAT will likewise explain its focus on industrial digitalisation, which is structured around an offer of intelligent developments using 4.0 technologies, with an aim to forging ahead in the automation of real manufacturing environments.
By way of an example in this respect, the company has developed Smart HMI, an intuitive interface aiding the operator and facilitating the use of the machinery, thus raising productivity.
This development allows quick and easy access to all the information on the status of the machine and its operation in a centralised fashion. Moreover, its design enhances usability and user experience.
Smart HMI helps optimise maintenance cycles as it shows the information relating to the status of the workpieces based on usage time, provides automatic notifications and maintenance instructions and improves reliability thanks to the self-diagnosis operations.
The development’s main functions include logical handling of control, documents on screen, assistance for identifying faults, monitoring of energy consumption, as well permitting the use of communication protocols.
The company has likewise developed a platform for capturing, storing and processing data called Data System which means the status of the machine can be monitored.
This development keeps the user informed of the situation and the working of the manufacturing process in real time, it lays down patterns, identifies tendencies, anticipates faults and implements intelligent maintenance strategies.