DANOBATGROUP presents its state-of-the-art machines, solutions and services at the BIEMH
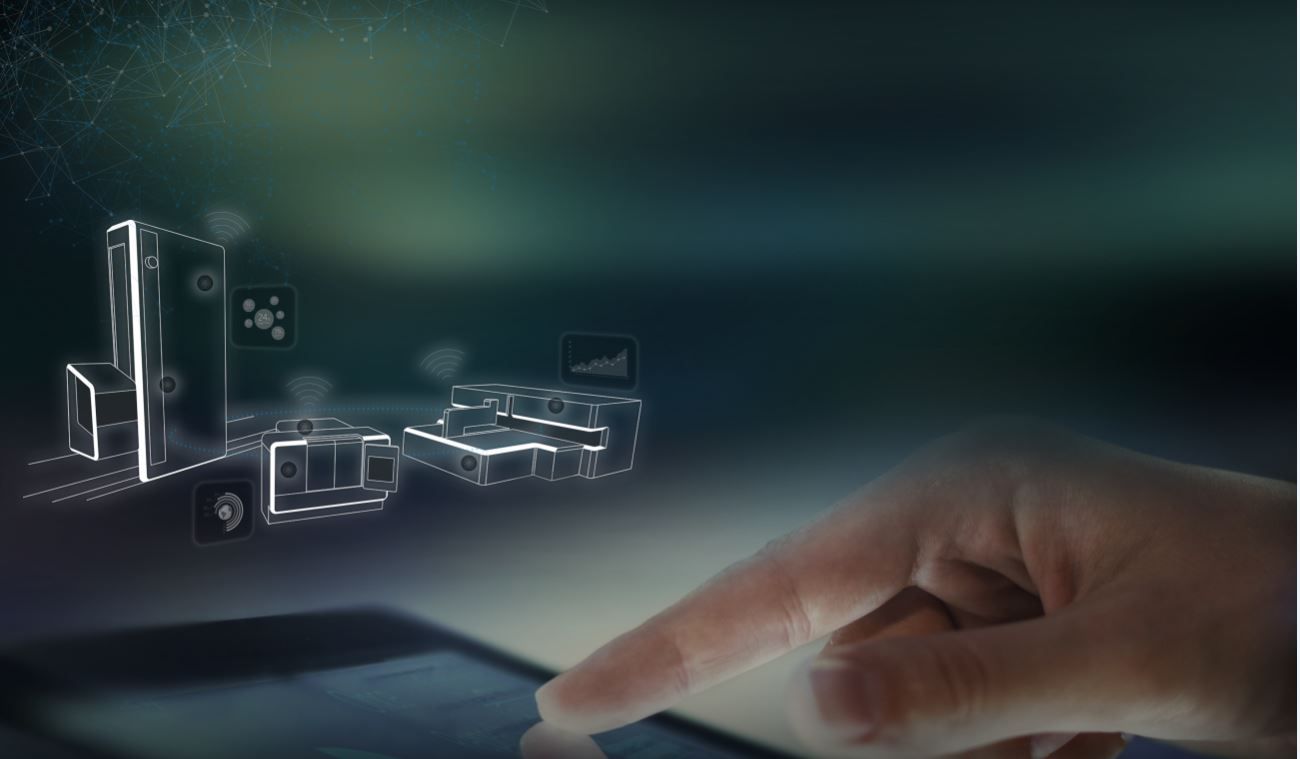
DANOBATGROUP will be present again at the Spanish Machine Tool Biennial (BIEMH), which will take place from 30 May to 4 June at the Bilbao Exhibition Centre (BEC), in Hall 5, stand C-11 displaying its firm commitment to cutting-edge technology with the latest solutions aimed at leading sectors.
At the 29th edition of the BIEMH, DANOBATGROUP will present the latest developments of its two renowned brands, DANOBAT and SORALUCE, showcasing its highly precise, reliable and high-output advanced machines designed to meet the most stringent demands in machining. All equipment includes top-quality, first-class parts to ensure rigidity, and dynamic and thermal stability throughout the entire lifespan of the machine. Advanced control systems secure that the demands for high speed and precision are met. Also on display are the advanced solutions for the manufacture of high added-value components for the most demanding industrial sectors. These solutions are the result of a solid experience in machining processes and close collaboration with leading companies in the sector on totally automated solutions installed in any part of the world.
The product is further completed with advanced services based on the latest information and communication technology that ensure maximum availability and support in programming, operation and maintenance of the equipment.
DANOBATGROUP will be present again at the Spanish Machine Tool Biennial (BIEMH), which will take place from 30 May to 4 June at the Bilbao Exhibition Centre (BEC), in Hall 5, stand C-11 displaying its firm commitment to cutting-edge technology with the latest solutions aimed at leading sectors.
At the 29th edition of the BIEMH, DANOBATGROUP will present the latest developments of its two renowned brands, DANOBAT and SORALUCE, showcasing its highly precise, reliable and high-output advanced machines designed to meet the most stringent demands in machining. All equipment includes top-quality, first-class parts to ensure rigidity, and dynamic and thermal stability throughout the entire lifespan of the machine. Advanced control systems secure that the demands for high speed and precision are met. Also on display are the advanced solutions for the manufacture of high added-value components for the most demanding industrial sectors. These solutions are the result of a solid experience in machining processes and close collaboration with leading companies in the sector on totally automated solutions installed in any part of the world.
The product is further completed with advanced services based on the latest information and communication technology that ensure maximum availability and support in programming, operation and maintenance of the equipment.
Under the slogan CONNECTING THE FUTURE, DANOBATGROUP will show the latest developments in the area of digital manufacturing and will reveal new solutions that make the factory of the future a reality today. Highlighting
- HMI - Human-machine interface, to improve the interrelationship man machine, through an environment that simplifies machine operation, includes support for programming and specialised machining cycles, facilitates the maintenance reducing down-times, and provides information on how to reduce power consumption.
- Data system, a set of services based on machine monitoring and Big Data to analyse the machining process and machine behaviour. You can use your tablet or mobile phone to check the status of the machine and, if necessary, optimise the process or anticipate possible failures.
- Intelligent components, devices integrated in the machine that, based on the information received from multiple sensors, act to improve the performance and precision of machines, optimise the process times, increase the lifespan of tools, etc.
- Control system, a computer application for full management of production lines. This system is independent of the manufacturer of the equipment, and hence it can be fitted on different types of machines; all information necessary to perform the given task is managed by the system: CNC programs, tools and tooling, etc. It can be included in other data management programs used on-site such as PLM, MES, ERP, etc.
In regard to machines, this edition of the fair presents the most advanced developments in grinding, turning, milling-boring, cutting and drilling technology and sheet metal processing machines of DANOBAT and SORALUCE brands.
Some of the exposed machines are new designs that in addition to basic essential properties such as reliability, accuracy and competitiveness, offer customers significant improvements in maintenance, ergonomics and safety in the work environment. Precisely because of this new concept applied to the new generation of machines, SORALUCE was awarded the prestigious Red Dot distinction, which is an international recognition for best product design. The SORALUCE FXR milling-boring machine stood out among no less than 5,214 nominations, an all time record, from 57 different countries, and won the Red Dot Award: Product Design 2016, one of the best products of this year.
DANOBAT LG-1000, accuracy and thermal stability
The DANOBAT LG-1000 interior and exterior horizontal grinder has, among other features, linear motor technology and direct transmission on rotary axes for grinding cutting tools, ultra-precision parts for the hydraulics industry and parts for the automotive sector among others.
The natural granite bed of the grinding machine and the linear motors slides provide the high accuracy and thermal stability required for these high demanding applications. It is also the ideal solution for non-cylindrical grinding.
The use of water-cooled electro-spindles makes it possible to combine conventional and high-speed grinding. This produces a maximum peripheral wheel speed of 120 m/s that covers the range necessary for grinding with conventional abrasives or super-abrasives with maximum torque.
SORALUCE FMT, multitasking for large workpieces
The SORALUCE FMT multitasking centre is a fine exponent of the new SORALUCE generation that blend ergonomics, safety and high output.
It is a large-sized multitask machining centre with full capability and functionality for turning operations as well as high power and torque in its universal milling-turning head. It is therefore capable of machining highly complex workpieces in a single set-up. The substantial savings in machining time that this provides make it more profitable for users in both series and one-off production.
This machining solution has an innovative design based on a flexible work area that is fully customisable. Customers can thus choose whether to use one or more work areas and incorporate additional rotary or/and fixed tables.
The machine features a full enclosure that provides easy access links to automatically opening doors that give full frontal and top access to the work area. This also facilitates the collection of chips and cutting fluid. To provide operators with better visibility, it also features large glazed areas. Easy operation, safety and cleanliness can be supplemented by the incorporation into the enclosure of fume exhaust systems. Additionally, the SORALUCE FMT shown incorporates an automatic robotic tool magazine with 150 tools.
The SORALUCE FMT multitask centre incorporates the innovative DAS System (Dynamics Active Stabiliser), patent pending. DAS technology, which is set to be a revolution in the machine-tool sector, consists of a device that actively increases the dynamic rigidity of machines, thus increasing cutting capability by up to 300% due to the reduction of the risk of chatter during machining process. The system increases cutting capability in general, improves surface quality and reduces the risk of tool breakages, increasing tool lifetime under extreme conditions.
The system has been tested on all types of machining processes, such as press heads, motor pole shoes and dies, and in all cases its use has resulted in reductions of up to 45% in the machining times tested.
The DAS system has won the European Quality Innovation of the Year 2015 and Best of Industry 2015 awards.
DANOBAT BM, demanding bending and high-value applications
In the field of sheet metal processing, it will be showcased the new automatic panel bender developed by DANOBAT, model BM, which ensures high productivity, minimizing machine setup times. The single tool bending concept on one hand and the automatic manipulation on the other, make the BM panel benders the ideal solution for large production volumes, both for small and large series. Ultimately, the DANOBAT BM panel benders are the best solution for all types of bends, from the simplest to the special and complex ones, and for high value-added applications.
DANOBAT is still committed to the development of special and innovative solutions in order to satisfy each of the specific needs of its customers. In this case, it will be launched at the exhibition the new LASER BLANKING machine, a flexible fiber laser cutting system in which the material to be processed comes from coil instead of sheet metal formats. It is a high productivity machine which combines each of the advantages provided by fiber technology apply to laser cutting with the advantages resulting from the use of metal coils.
In addition, DANOBAT continues to develop special and customized solutions for specific sheet metal applications, such as metal doors, silos, household applicances and kitchenware, metal furniture, etc. These solutions are the result of the years work carried out by DANOBAT together with its customers.
DANOBAT HDS8A robustness and precision
The half or fully-automatic HDS8 saw is designed to cut large capacities up to 800mm. Robustness and accuracy characterise the DANOBAT HDS horizontal cutting saw to ensure maximum productivity and a first-quality cut. The robust columns and head manufactured from one single piece cancel out all vibration during the cutting operation.
The material is clamped on both sides of the band, guidance is automatically adjusted to the width of the material and the mobile arm is hydraulically locked during the cutting operation.
DANOBAT COMPOSITES, production automation for structural parts
The ADMP® (automated dry material placement) technology will also be on display, a technology developed by DANOBAT for the automated manufacturing of structural parts of composite material. The ADMP® technology is highly productive and versatile and offers great advantages as it is possible to accurately and rapidly lay a wide range of dry materials, such as tapes, NCFs and wovens.
LATZ cutting tools, high precision, reliability and cutting-edge technology LATZ cutting tools
The stand will also have a specific area for LATZ cutting tools that stand out because of their high precision, reliability and state-of-the-art technology.
Among others, standard and special HSS and Carbide cutting tools for the main industrial sectors (aeronautics, automotive industry, etc.) will be exhibited.