New coil fed fiber laser cutting system
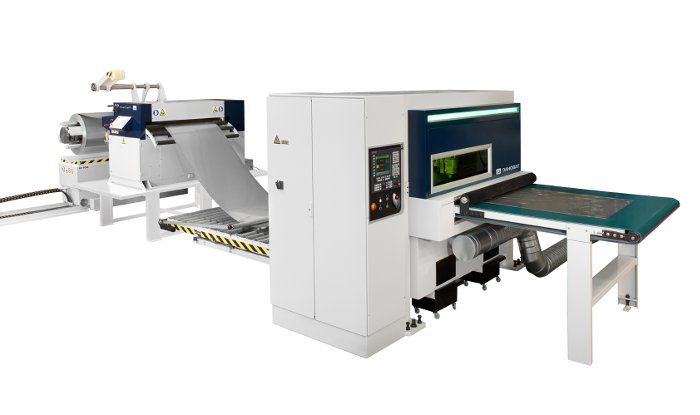
The DANOBAT Sheet Metal division expands its fiber laser cutting product line through the introduction of coil fed systems, whose primary goal is to achieve significant savings in the materials to be processed and an increase in productivity as a result of reduced machine downtimes.
DANOBAT remains committed to developing unique and innovative solutions in order to meet its customers´ specific needs. A flexible fiber laser cutting system, coil fed instead of sheet fed, has been developed.
This highly productive machine takes full advantage of all the benefits offered by fiber laser cutting technology (efficiency, speed, versatility, minimal maintenance, etc.), as well as the benefits arising from the use of metal coils (up to 15% savings in materials cost and improved sheet utilisation).
Product customisation
The system is comprised of a sheet feeding line and a perfectly integrated laser cutting module that work together for continuous operation. The feeding line is equipped with an uncoiler which unrolls the coil, a straightener which removes the sheet´s contours and internal stresses, and a looping pit which stores the straightened material for processing. The laser consists of a fiber laser generator and a cutting head which moves in sync with the sheet to obtain the desired geometries. The exit of the cut pieces can be automated using different systems—robots, stackers, etc.—depending on the customer´s needs.
Laser cutting head
The system includes the new "ProCutter" cutting head from Precitec, which has been designed to achieve greater control of the cutting process, as it is possible to monitor the state of the head at all times. A mobile phone can be used to display parameters such as:
- Optics temperature: Lens, protective window, and collimation lens
- Pressure: Gas cutting and purge
- Protective window pollution
- Working distance control
Multiple heads
Due to its modular design, multiple heads can be integrated into the solution, in order to exponentially increase the cutting process´s productivity. The workload will be consequently distributed among the heads.
Applications
As this system has a wide range of potential applications, it is essential to carefully analyse what the customer´s needs are on a case-by-case basis: types of materials, cutting thicknesses, required productivity, characteristics of the pieces, etc.
This machine can be used in different fields of application, such as:
- Automotive: Structural parts of vehicles.
- Tableware: Discs for pots, frying pans, paella dishes, etc.
- Metal silos: Roof sections for metal silos
- Light fixtures: Light fixture bodies