DANOBAT exhibits its latest precision solutions at the GRINDTEC
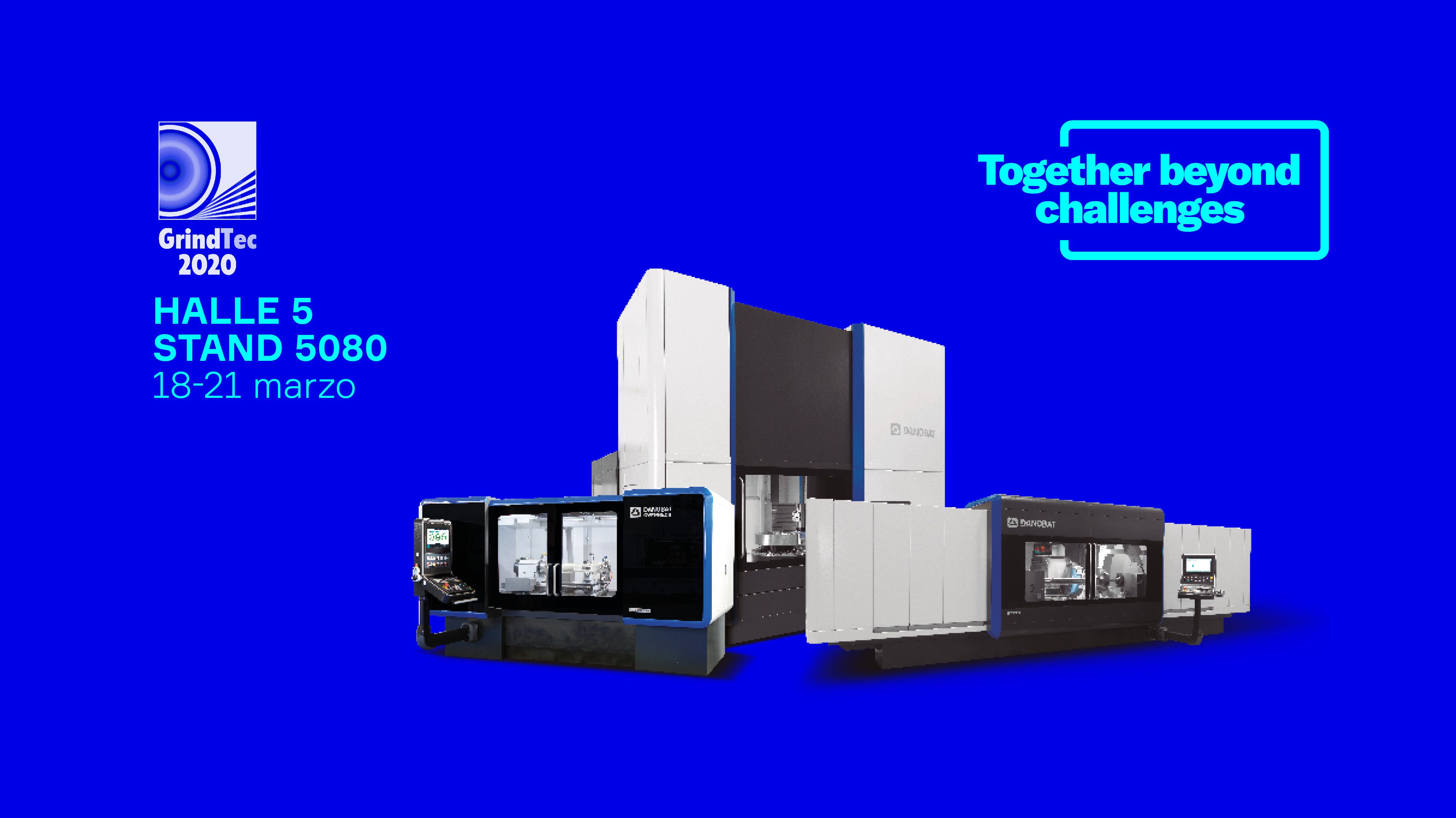
-
Danobat will present in hall 5 stand 5080, three of its precision machines: Danobat CG-1000, MIKROTURNGRIND 1000 from Hembrug and the Danobat-Overbeck IRD-400 for internal grinding.
-
Danobat, Danobat-Overbeck and Hembrug, 3 leading brands in precision due to their experience and expertise.
Danobat, experts in the generation of innovative technological and high added value solutions for the industrial manufacturing, comes to GRINDTEC with customized, precise and high value-added technology. The fair will be held from 18 to 21 March at the Messe de Ausburg and will feature the solutions from Danobat, Hembrug and Danobat-Overbeck.
To showcase the expertise, Danobat will be exhibiting in hall 5 stand 5080, the Danobat CG-1000 machine for external grinding, the MIKROTURNGRIND 1000 multitasking machine and the IRD-400, an internal grinding machine for high geometric complexity operations.
DANOBAT CG-1000: HIGH PRODUCTIVITY WITH THREAD GRINDING CAPABILITY
The Danobat CG-1000 machine, result of collaboration with customers, is a best value for money, high production grinding machine.
CG-1000 is designed for external operations and stands out for its ability to grind threads. It has a wide variety of wheels and can be applied for an extensive variety of applications. The grinding machine has a structure that stands out due to its rigidity, allowing it to successfully meet the customer’s high productivity demands. The wheel head reaches a maximum peripheral speed of 80 m/s covering the necessary range for grinding with conventional abrasives. As a result, cycle time is considerably reduced, doubling wheel life, and process stability is guaranteed.
The CG-1000 features a post-process measuring unit to verify the precision tolerances required in final machining, which reduces cycle time. Like all CG machines comes also with the intuitive, in-house developed and user-friendly software Danobat DoGrind+.
The CG machine range is designed in such a way that a 24/7 production with only minimum service intervals is guaranteed. In addition, Danobat maintains a large stock of OEM parts. These are delivered quickly and directly without the intervention of secondary parties. All this contributes to the high annual machine availability close to 100%.
Danobat also offers turnkey, automated solutions for the CG machines consisting of standard in-house developed modules. These compact, efficient and cost-effective solutions ensure a further boost in productivity. Apart from standard integrated automation solutions, external turnkey systems can also be provided in order to meet specific customer requirements.
DANOBAT-OVERBECK IRD-400: HIGH-PRECISION GRINDING IN HIGHLY COMPLEX GEOMETRIC PIECES
The IRD-400 grinding solution offer that Danobat-Overbeck takes to the fair includes internal, external, radius and non-round grinding. In this case the presented application shows the capability or option of this machine to grind as well between centers. The flexibility of this grinding machine enables it not only to grind workpieces clamped only by a chuck but as well as tailstock.
The main advantages offered by this development are the maximum flexibility obtained for pieces with high geometric complexity and high versatility.
The grinding machine achieves highly accurate finishes thanks to its B0 axis which swivels up to 91 degrees. Axis control means complex internal shapes can be made using one single wheel and in one contour line, thus maximizing productivity.
With this model, the spindle turret includes a measuring probe integrated in the software with which the starting position of the workpiece can be detected. This ensures that, on the final finishing run, the system reaches the required measurement with precision. In round contours, roundness deviations of 0.5 µm can be reached.
Another of the peculiarities of this development is the high degree of exact synchronization of all the movements of the axes, including the rotation axis of the workpiece (C0), thus enabling eccentric grinding. This feature means that complex geometries can also be machined with the aid of coordinate grinding, and square, rectangular or freeform shapes can be made to great precision.
HEMBRUG MIKROTURNGRIND 1000: THE SOLUTION THAT COMBINES GRINDING WITH PRECISION TURNING
The MikroTurnGrind 1000 hybrid machine combines the advantages of hard turning and finish grinding in one machine. With the MikroTurnGrind 1000, manufacturers can apply the most suitable process for each surface to be machined, all in one set-up without the need for multiple machines.
To ensure sub-micron workpiece accuracy, the MikroTurnGrind 1000 comes as standard with a 4,000 rpm hydrostatic work-spindle with runout of < 0.1 micron (TIR), hydrostatic X and Z axis slides having repetitive accuracies of ± 0.1 micron. The wear-free, hydrostatic bearings ensure that the machine will continue to deliver the same level of accuracy after 20 or 30 years. The MikroTurnGrind 1000 utilizes a B-axis that offers optional space for a turret with 8 fixed VDI 30 tool holders, an external grinding spindle with a 300 mm diameter grinding wheel as well as an internal grinding or milling spindle.
The MikroTurnGrind 1000 offers unsurpassed accuracies in both hard turning and finish grinding.
DANOBAT, DANOBAT-OVERBECK AND HEMBRUG, 3 LEADING BRANDS IN PRECISION
Danobat with more than 65 years offering solutions to the industrial manufacturing; Danobat-Overbeck with a century of history in the development and manufacture of internal, external, radius, face and non-round grinding and Hembrug, one of the pioneers in Europe with more than 100 years of experience in precision turning, shape a company with innovative and high value-added technological solutions that position them as leader in precision machining.