DANOBAT reinforces its specialization in the oil&gas industrie with BGM
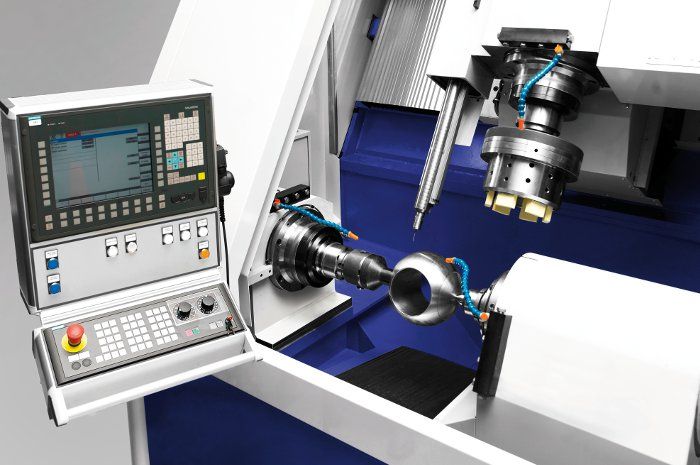
The Oil & Gas sector has always been a highly demanding industrial market. The shortage of available energy resources, increased activity in deep waters, high pressures, low temperatures, extreme conditions, etc, in addition to the absolute need for high productivity and reliability make it a challenging industry in a complex world.
DANOBATGROUP has a business area specialized in turnkey solutions for the Oil & Gas industry. The company has been working together with the world´s leading manufacturers such as Aker Solutions, Cameron, Metso, Mogas, NOV, Tenaris, Tpco and Vallourec among others, providing high value-added solutions in the manufacture of parts such as pipes, couplings, high pressure valves, ball valve seats, balls for ball valves, and more.
In this occasion DANOBAT comes up with a solution for the machining of balls for ball valves: the DANOBAT BGM mahine. The BGM is able to machine diameters up to 2100 mm and materials with a complex machinability such as stainless steel, duplex and superduplex HVOF. Its long-standing experience in the field of grinding technology is materialised in this product family. Machining is performed with a segmented grinding wheel and the power spindle ranges from 25 to 85kW.
DANOBAT BGM machines govern the force exerted on the ball during the machining process, thus guaranteeing the surface finish requirements set by the client. Also, centering of the workpiece is performed by controlling the two axes to adjust the height of the wheel spindle to the horizontal work spindle axis.
Furthermore, during the machining process, measuring can be done before and after grinding with the purpose of obtaining a more controlled result. The operator can monitor and make adjustments to the entire process through the graphic 12" NC panel with CNC or PLC technology and specific software for grinding balls of ball valves.
The bed is also designed and optimised to achieve the best results, facilitating the removal of residues produced during the grinding process so as not to damage the workpiece or the machine components. Even so, both the linear axis and the spindles are protected against residues with pressurised metal bellows to ensure the durability of the BGM.
These machines offer several possibilities for customisation to suit the needs of each customer and each process. Optional equipment includes, among others, turning capability, diamond dressing and automatic tool changes. These configuration modules facilitate several automation processes and as a result enhance the productivity of the machine.
However, DANOBAT solutions for this specific sector do not end here. Apart from the earlier mentioned system, the company offers a comprehensive solution for machining the ring of the valve seat of between 100 to 1700 mm, and its manufacturing plant in Germany, DANOBAT-OVERBECK, manufactures machines such as the IRD model which has been conceived to grind smaller valve balls.