Danobat vertical lathe machines vs. other brands
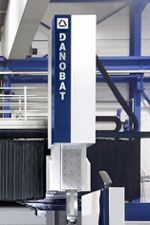
On a continuous challenge of innovation, the Danobat Vertical Turning Centre is a world reference. First class parts are used in our Danobat Vertical Lathes for high precision machinig, low cycle time and maintenance costs as well as a lower energy consumption than other brands. The cinematic chain of the Danobat Vertical Lathes is designed to increase the efficiency of all the machining processes. All the power and torque of the main motor is transmitted to the main spindle without belt slides over the pulleys. The spindle speed and performance is controlled by a high quality encoder for the the C axis. This encoder allows very high positioning accuracy and repeatability. To ensure the quality of all our machines, Danobat performs laser tests on all produced vertical lathes assuring high quality results. The gearbox, developed entirely by Danobat technology, has inmediate availability with Danobat stock in case of damage. This cinematic chain allows a support of 105 kW with perfect performance and long machine life.
Danobat Vertical Turning Centres are engineered to include the latest innovations of the market to offer the best solution for each customer. For the vertical lathes, Danobat uses one sole cross roller bearing of a bigger diameter than other brands, which gives more stability and loading capacity to the machine. It has a high capacity for tilting moment that gives a good solution for excentrical loads. Other competitors that use two independent bearings requires the bed to have two housing machined for those bearings. This will cause geometric doubts that will decrease the life and correct working of the bearings. Danobat vertical lathes are designed to provide great stiffness thanks to the short distance between the rotary table and the bearing. Danobat chooses very carefully its suppliers, that´s why the bearings are provided by the best bearing manufacturer in the world. When deciding the type of guides of X and Z axis Danobat has a clear choice of linear guides in order to avoid the stick slip effect and guarantee high speeds. Instead of the commonly used ballscrew for the X axis, all Danobat VTC models are equipped with a double rack & pinion system that absorbs the vibrations and produces no backlash nor deformation. This Danobat system is a easy to maintain in-house development that offers an effective and flexible solution to the customer. The double rack & pinion system allows the RAM head to work on both sides of the part and the machine flexible design is compatible to add two automatic tool changers and a second RAM if needed on the future. The geometrical adjustment of the machine is easier with Danobat thanks to the double saddle and swivel. In case of a collision the swivel will spin over the saddle and the machine will face no damage. Danobat challenges itself to offer the most effective and customized solution to the customer using the ultimate technology on the market.