Production of parts with hirth and curvic couplings in a multitasking grinding machine
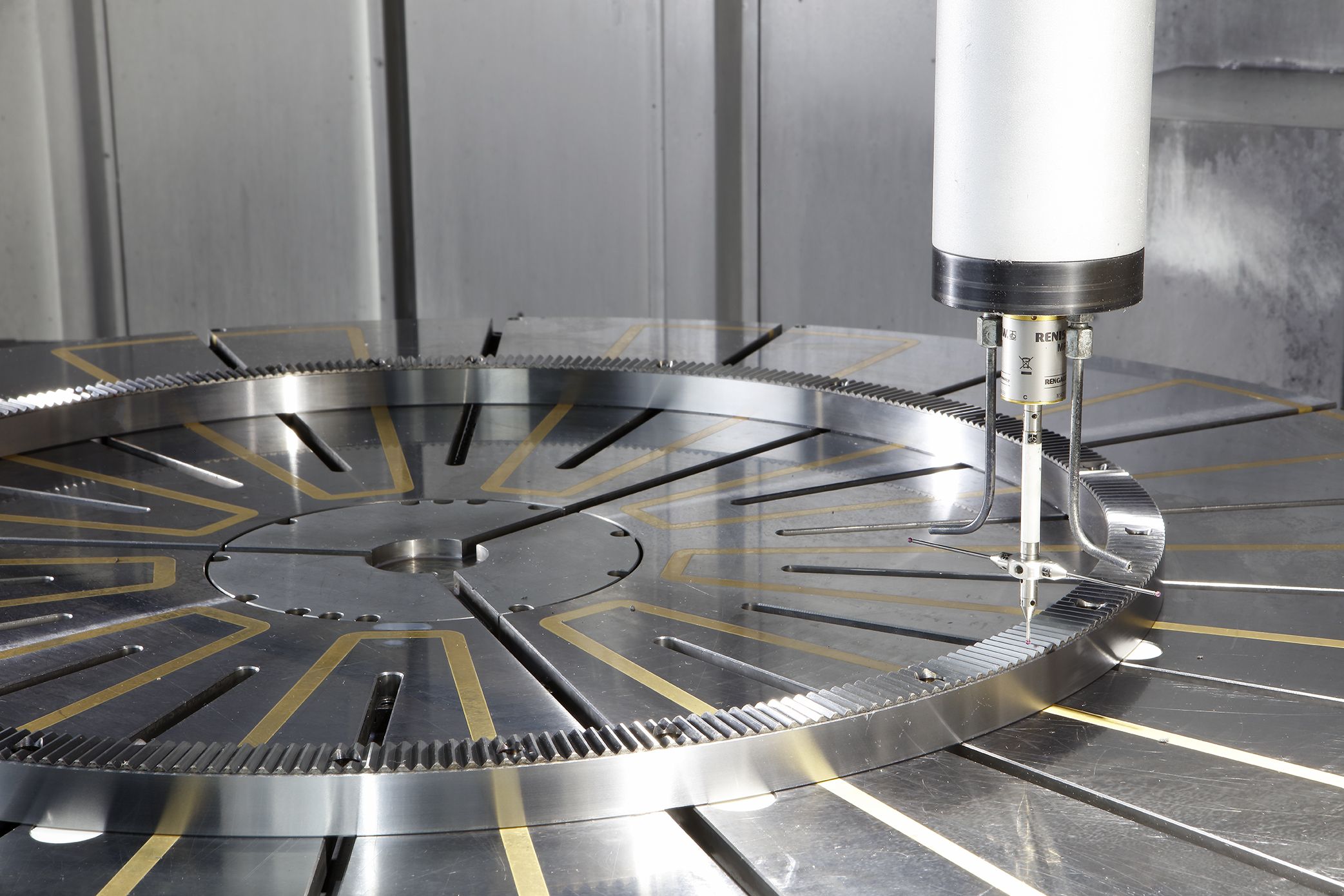
The DIVIPREC company specialises in precision grinding and machining. It is a market leader in the manufacture of rings with HIRTH and CURVIC couplings and exports more than 50% of its production to customers in the aerospace and machine tool industries.
The requirements, whether the parts are supplied by its customers or are manufactured from skretch by DIVIPREC, are high. “Our customers have high expectations when it comes to precision and accuracies, surface finishes and delivery times, thus we are constantly optimizing and improving our manufacturing processes to meet the ever-increasing demands”, Xabier Rementeria, Managing Director of DIVIPREC confirms.
This philosophy of continuous improvement has driven the company to develop a new production system that achieves the levels of precision required by their customers. This search for excellence strategy also allowed DIVIPREC to detect the need for a multitasking solution that would be capable of carrying out several operations and thereby optimise their production processes.
To achieve this dual goal, obtaining maximum precision and integrating several processes in a single solution, DIVIPREC has trusted in the capabilities of Danobat, a manufacturer of precision machine tools and advanced production systems. The company has developed a customised solution to cover all DIVIPREC’s requirements.
A stable alliance
This is the fourth machine Danobat developed for DIVIPREC, a highly specialised grinding company, further solidifying the close collaboration between the two companies. “We have been working with Danobat for over twelve years and have first-hand knowledge of their capabilities and the level of precision that go into their products and solutions. The results have always been good because in Danobat, we found a technical team and partner that is listening to our needs and requirements. We challenge each other and we can always count on them,” Mr. Rementeria pointed out.
After a year-long process for the development of the solution and after strict validation tests with very narrow tolerances, Danobat has delivered a new vertical VG-1500 machine, capable of manufacturing parts with diameters ranging from 50 mm (2”) to 1500 mm (60”). The solution also performs multiple tasks in one clamping, resulting in tighter tolerances and runout for DIVIPREC’s entire part range.
With the VG-1500, DIVIPREC has improved its capacity to grind flat surfaces, diameters, cones, shapes and Hirth and Curvic couplings. The machine is also equipped with a system that measures all the surfaces with a contact probe so the part can be validated before it is removed from the machine. Among other relevant features, the VG-1500 has six controlled axes. Four of these axes are linear: Three are for grinding and one for dressing positioning and interpolation, while the two remaining axes are rotary axes driven by torque motors. One of the rotary axes is the workpiece table, which corresponds to the inclined position of the table and has a precision of one arc second, which is one of the requirements for the manufacture of Hirth couplings. The second rotary axis is the B axis, which has three heads and a measuring system and is used to select the work tools.
The VG-1500, with its many innovative features, reflects a solution that was developed in close cooperation between both companies and meets the objective to optimize DIVIPREC’s production processes. Among other benefits, the machine can be used to manufacture high-precision Hirth couplings, one of the core competences of the company. Moreover, the new solution increases the work envelope for parts up to 1.5 meters (60”) while achieving superior precision compared to how parts were processed previously.
The machine has been operating at full capacity during two shifts since September 2020, working 16 hours a day. It is located at the new pavilion built by DIVIPREC, inside an air-conditioned room, where the temperature is kept at a constant 20 degrees. This is only one of many measures taken to achieve the level of precision required by their customer.
The results speak for themselves. “The machine has been working for several months at full capacity, consistently meeting all the acceptance requirements and very narrow tolerances. Once again, Danobat has demonstrated its superior capabilities, while also offering constant support and assistance in our effort to continuously improve our operations”, added the Managing Director of DIVIPREC.
A highly qualified team
To develop this solution, Danobat placed a highly qualified team at the disposal of DIVIPREC, consisting of engineers and software experts who have provided their know-how for the development of the process and the architecture of the grinding machine. This is the technology behind the machine tool manufacturer’s leading position in the market, with more than 10,000 references installed and a large international presence.
About DIVIPREC
The DIVIPREC company specialises in precision grinding and machining of components for the aerospace industry; it has its own products and focuses on the manufacture of high-precision HIRTH and CURVIC couplings. Its main goal is to provide maximum quality and perfection for its products, along with service that is reliable, fast, efficient and adds value so it can comply with the most demanding expectations of the market. The company is SO 9001:2015 certified and their products can be found throughout Europe, the USA and Asia.
About Danobat
Danobat develops machine tools and processes, intended for high-tech industries and customers that demand highly productive, accurate and reliable solutions.
The company’s offer consists of advanced machines that ensure high precision, reliability and productivity and are designed for the most demanding machining processes. The company also develops advanced systems for the manufacture of high added-value components, developed in close collaboration with companies that are leaders in their sector. The goal is to generate lines that are fully automatic and end-to-end solutions that cover all the stages of manufacturing processes.
The company has a strong international presence and counts on production plants Spain, Holland and Germany, as well as centres of excellence in those countries and in Italy, the USA and China.
Danobat belongs to the Danobatgroup, an industrial group that employs 1,300 people and invests 8% of its turnover in R&D&i projects.