DANOBAT has developed a high precision multi-disk cutting solution for the automotive, oil&gas and bearing manufacturing sectors
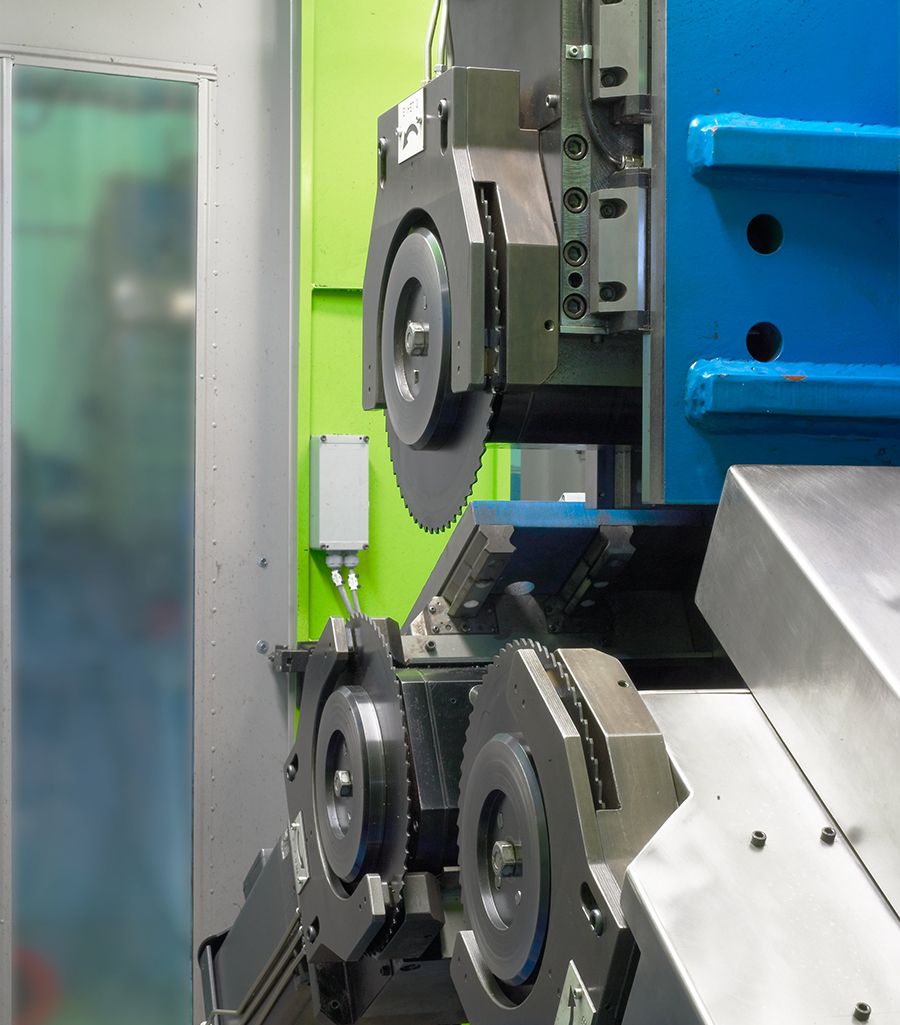
-
The machine-tool manufacturer has designed a high-output fully automated flexible system which can be adapted to clients´ needs.
-
The solution, developed for an iron and steel multinational company, facilitates cutting high added value steel tubes while minimising material waste.
DANOBAT, the machine-tool manufacturer, has developed a high-precision multi-disk cutting solution aimed at cutting high added value steel tubes used in strategic sectors such as oil&gas, automotive or bearing manufacturing.
The solution, conceived for a steel industry multinational company, facilitates cutting steels of different qualities and diameters within 60 mm to 280 mm, with a maximum thickness of 40 mm and lengths ranging from 25 mm to 400 mm. However, DANOBAT´s system is defined by its high flexibility to adapt to other parameters depending on the client´s requirements.
This solution is envisaged to be integrated into the production plant Manufacturing Execution System (MES). Its operation is fully automated and is equipped with a load bed which places tubes in the exact position ready to start cutting operations. As a result, the three machine disks, mounted on a rotating head assembly, can start the cutting operation.
One of the main technological advantages of this solution is the rotating capacity of the disks which makes cutting possible exclusively to thickness. Thanks to this, times can be reduced while productivity is significantly increased.
In addition, the device boasts a robotised exit system which displaces cut tubes to the threading line, to continue with the subsequent machining phase or proceed to storage.
The solution, equipped with DANOBAT´s proprietary software, enables communicating with the production plant central control system, which sends production orders directly to the device.
DANOBAT´s development integrates Industry 4.0 technology, fits within the zero defect manufacturing framework and complies with minimisation of kerf requirements; i.e. reducing the amount of waste material generated in the cutting process.
This is a global solution including the study of process characteristics, units and peripheral devices. This smart fully-automated solution offers high output and operates at high speed. High quality results are safely obtained while material waste is minimised.
Furthermore, this system can be integrated with other equipment already installed at the plant, with the aim of working on-line but also facilitating already cut parts are palletised to be stored and delivered to another destination.
Synergies for saw development optimisation
This development falls into DANOBAT´s commitment to move forward in the design of technologically-advanced high value-added cutting solutions.
In this context, the machine-tool manufacturer acquired the Finnish company Plantool, specialised in the design of circular saws and high reliability and precision cutting solutions, fitted with state-of-the-art control systems.
The integration of Plantool technology in the development of DANOBAT integral automated solutions has materialised in the production of cutting-edge systems capable of adapting to clients´ needs.