SORALUCE is undertaking a research and development project to increase its competitiveness through a framework of new technology generation
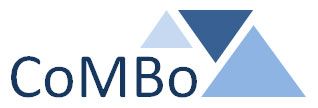
SORALUCE, company integrated in DANOBATGROUP, is currently working on the “COMBO' project in collaboration with IK-4 IDEKO Technology Centre, to generate:
- New technologies for increasing precision, productivity and functionality
- Increased milling and boring machine manufacturing competitiveness through a technology development framewor
COMBO is a 2 years project .
Leading-edge manufacturers need to compete on both the traditional markets . On the emerging markets, however, the leading-edge manufacturers have to compete with low-cost producers. Obviously, the price factor is present on all the markets, but technology differentiation is becoming established as the only resource enabling competitiveness to be maintained. This project will allow SORALUCE to take on the development of a set of innovative, cutting-edge, differentiating technologies that will help it achieve world technological leadership in the milling and boring sector by 2016, as proposed in its strategic reflection. This involves achieving three previous landmarks:
- Catering to demanding market requirements .
- Providing a clear technology differentiation with respect to the current state of the art.
- Increasing SORALUCE’s market share in the milling and boring sub-sector.
This project thus materialised as a result of a collaboration agreement between the milling and boring machine manufacturer SORALUCE and the IK4-IDEKO technology centre, specialists in machine tools and industrial manufacturing and production technologies. The aim of this agreement is to define and approach a development and technology transfer framework between the two parties, in order to boost the company’s competitiveness in Spain and abroad, which will generate financial profit for its surrounding area. To respond to the demand, the technology development forming part of this project is grouped into the following areas:
- Increased precision: compensating errors of all kinds directly affecting the final precision to be obtained from the parts. Precision requirements are constantly increasing as regards both dimensional accuracy and surface finish quality. New advanced measuring systems and mathematical models will therefore be developed to compensate critical errors and enable technology differentiation.
- Increased productivity: systems will be developed enabling active control of cutting conditions, the use of new, innovative materials in critical parts of the machine will be tested and the multifunctionality area will also be developed, while contemplating aspects of energy efficiency and eco-design.
- Increased functionality: software-based systems will be developed to integrate knowledge to the machines, with CNC operator aid and new control and diagnosis functions.