SORALUCE optimizes NASOSENERGOMASH´s production process
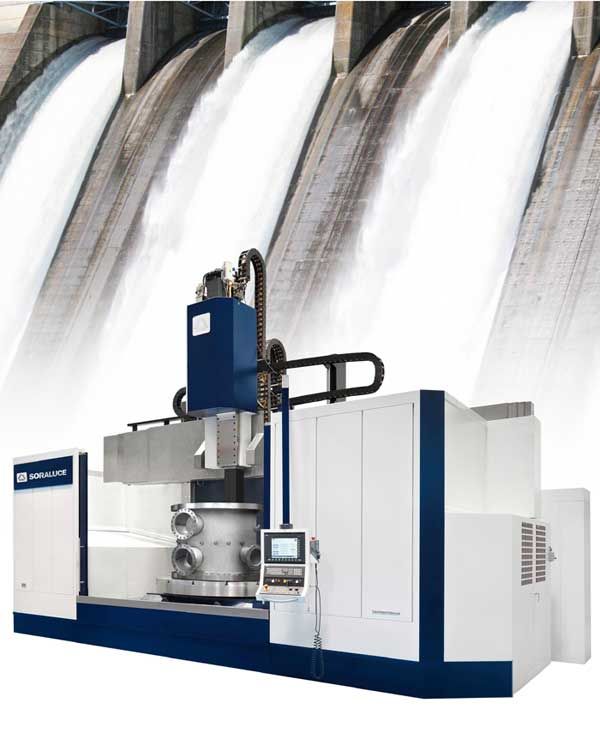
NASOSENERGOMASH Pump & Power Engineering Works Sumy is one of the Ukraine’s most important industrial companies, specialising in pump manufacture for the nuclear, oil & gas, thermal power and water supply sectors. Its state-of-the-art pump design, manufacture, processing and testing facilities are the base from which it designs and launches new pump models to meet the most rigorous demands of the sectors it supplies. NASOSENERGOMASH has recently purchased three machines from DANOBATGROUP: a VTC-1800 vertical lathe, a VTC-3200 vertical lathe and a FR-10000-W travelling column milling-boring machine, to optimise its production process and the precision of its components.
We spoke to Vladimir Kushko, Nasosenergomash’s Technical Manager, about the advantages of using the VTC-3200 vertical lathe in the production process. Q: What kinds of components do you machine? Vladimir Kushko: We use the vertical lathe for machining pump bodies for the nuclear power sector, pumps for oil transportation and pumps for electric power stations. Q: How complex are these components? Vladimir Kushko: Their complexity lies in the precision of their parts. The largest diameters have to be within 0.01 mm tolerance . Machine precision and reliability are two very important aspects required by the sectors we work for, and high productivity is also essential. Q: How has your pump body production improved with the new VTC-3200 vertical lathe? Vladimir Kushko: There has been a great improvement as regards precision and productivity. Previously, the pump bodies were processed on six different machines to undergo all the machining operations required. With the VTC-3200, all the operations are carried out on just one machine and with a single clamping process. This has increased our productivity, reduced the idle time needed for part clamping, and it has improved precision as there is only one clamping process. The machine also includes a head with four turning positions, allowing four tools to be used with no stoppage times for tool change, and this optimises the machining times. Q: What are the main operations performed on the VTC-3200? Vladimir Kushko: The basic operations required by the pump bodies are turning, drilling, milling and threading. The VTC-3200 turning centre is equipped with a variety of different heads and we can carry out all these machining operations and other on the same machine and with a single clamping process. Q: How do you rate DANOBATGROUP’s work on this project? Vladimir Kushko: DANOBATGROUP has been an exceptional partner. We explained our machining problems and our requirements to them and DANOBATGROUP proposed a very precise, highly productive solution. They showed great know-how and flexibility, adapting to our specifications and putting forward improvements that have a very positive effect on the end product.