SORALUCE displays avant-garde innovations and technological developments during Technology Days 2015
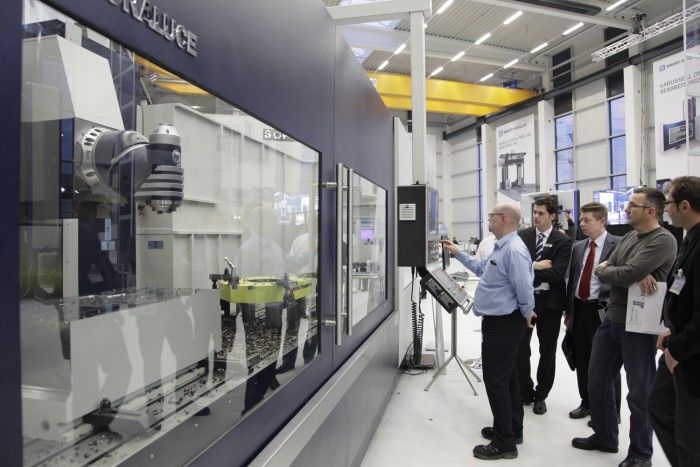
SORALUCE held the 5th edition of Technology Days at the Excellence Centre BIMATEC SORALUCE from 17th to 21st November 2015, to experience the latest technologies and developments by SORALUCE in real machining conditions, highlighting the new SORALUCE product generation, innovative DAS system (Dynamics Active Stabiliser) and latest developments in Industry 4.0.
The European manufacturer vouches its leading position in innovation, customer orientation and value generation, staying close to customers, providing expert advice, technology going through permanent evolution, consolidated solutions and a wide range of services with added value.
Specialists in milling, boring and vertical turning have demonstrated last technologies and developments in real machining conditions through the Technology Tour; a tour through eight different milling, boring and multitasking machines on display with different live demos in each one.
During Technology Days, SORALUCE, BIMATEC SORALUCE (Centre of Excellence), IK4-IDEKO(R&D Centre) and its partners have arranged several Workshops on different topics focused on improving customer’s productivity, profitability and operations, offering the best opportunity to learn from the very best experts in each topic.
New SORALUCE Generation
The new generation, displayed in a wide range of machine models, is the expression of SORALUCE’s values: reliability, precision and competitiveness. Within these concepts, customers find huge improvements in maintenance, ergonomics, high dynamics and safety in the work environment.
The New SORALUCE Generation is based on a complete revision of the machine from the user’s point of view focusing on improving operation efficiency and developing a Total Machine Concept.
The Total Machine Concept takes into account the machine but also the complete working area. All the interactions of the operator with the different machine elements are analysed for an optimal implementation.
The evolution taken in design makes it easier to operate and maintain the machine. SORALUCE has launched onto the market a new generation of machines which have a more ergonomic working environment and maximum protection for the operator.
During Technology Days, SORALUCE has presented four examples of this new concept of integral design focused on improving profitability and greatly accommodating the working environment for the operator; a travelling column milling-boring machine SORALUCE FXR with great dimensions and machining capacity, a multitasking SORALUCE FMT machine combining the best of milling and turning capabilities, a travelling column milling machine SORALUCE FL with high dynamics and the fixed table travelling column milling centre SORALUCE SLP noted for its large capacity and ergonomics.
Innovative DAS System (Dynamics Active Stabiliser)
Two of the machines shown on the Technology Days, the travelling column milling-boring machine SORALUCE FXR and the travelling column milling machine SORALUCE FL, are equipped with the new DAS system (Dynamics Active Stabiliser), patent pending. This system is the result of the joint effort between SORALUCE and its research centre, IK4-IDEKO together with testing at BIMATEC-SORALUCE, Centre of Excellence of the brand in Germany. This joint R+D+i effort , where users’ suggestions have specially been taken into account, has brought to life a system capable of increasing the dynamic rigidity of the machine in real time increasing the machining performance by up to 300 per cent. This reduces the classic regenerative effect of the chatter when machining. The DAS system improves milling capacity and surface finishing quality while reducing the risk of breaking tools, increasing tool life under extreme machining conditions.
This new development consolidates the reputation of SORALUCE as the Home of Innovation, a company where innovation is born from and for the customers, keeping in mind their needs and developing technology that matches with their manufacturing challenges.
Industry 4.0, Smart Manufacturing Solutions
The on-going digitization in the machine tool field is opening up new possibilities for the manufacture of more intelligent products and solutions and therefore more efficient. Digitalization is the key to increasing productivity, efficiency and flexibility through innovative software developments.
SORALUCE, in its firm commitment to the Smart Factory, responds to the initiative Industry 4.0 driven by the German Government with the development of utilities to serve the most advanced users.
SORALUCE develops value-added services taking advantage of opportunities provided by the new electronic, information and communication technologies, with the aim to create Smart Manufacturing Solutions characterised by adaptability, resource efficiency and ergonomics, thus updating its products to the new Industry 4.0 environment.
These developments provide greater availability and possibility of data processing and analysis, remote communication possibilities in real-time and high performance capacity (adaptation, flexibility) of the machines, resulting in functionalities, capabilities and services of a higher level, making machine operation and management really straightforward.
SORALUCE has developed three software packages in the environment of Industry 4.0:
- ACCURACY Pack: Machines incorporate intelligent systems which improve accuracy and increase productivity
- OPERATION Pack: User-friendly and intuitive interface that improves advanced operation and aids programming to simplify machine operation
- MONITORING Pack: Remote access to the machine state to track the evolution of the key variables which enables optimizing the operating conditions and the prevention of possible failures
SORALUCE is working on the solutions of the future where the operator can track the complete machine from any location using a smartphone, table or PC.
The Technology Tour
SORALUCE has introduced the new innovations and developments in real machining conditions through a Technological Tour where eight different milling, boring and multitasking machines were displayed with different live demos that included impressive examples of the use of the DAS technology.
Demonstrations also showed other technologies applied to SORALUCE machines such as the dynamic CNC ram balance system, patented by SORALUCE, which guarantees the geometrical accuracy, straightness and parallelism, of the ram traverse over the Y and Z movements. This system, consisting of a CNC controlled electromechanical system assembled within the vertical saddle, particularly increases precision when the machine is equipped with the automatic head changing system, as it allows for accurate correction of the mechanical ram deviation regardless of the different weights of individual milling heads.
The modular quill spindle was another example of a worldwide patented system unique on the market. The system fully automatically interchanges the quill spindle with the other heads, thus enabling different quill spindles with different diameters and lengths likewise all necessary milling heads to machine components. Compared to traditional quill solutions, the exclusive SORALUCE modular quill spindle enables the same distance between quill spindle and milling heads to be upheld, enabling 5-sided machining in the same set-up without any additional positioning of the work piece at a long distance from the machine.
SORALUCE also displayed their new dynamic head calibration system of its heads, DHC. It is a self-calibration system which increases head positioning precision at any point in the space. The auto-calibration cycle is a simple process requiring only a master standard, a measurement probe sphere and the software provided by SORALUCE.
SORALUCE FXR-W 16000, productivity for large component machining
SORALUCE FXR-W 16000 floor type milling-boring centre offers high versatility and productivity for large component machining. The FXR-W milling boring centre is a multi-purpose milling- boring machine. Its rigid stable design provides the highest precision and productivity benefits when machining large components.
The machine modular design offers remarkable versatility and can be equipped with a large number of optional accessories and wide range of milling-boring heads, enabling machine adaptation to customer needs with high efficiency and precision. The machine responds to multitasking and versatility requirements likewise the demand for finishing work pieces in a minimum number of set-ups.
It is the ideal solution for machining components belonging to sectors like: energy (wind-power, gas, nuclear), shipping, capital goods and precision engineering, ensuring the highest precision, productivity and reliability for heavy duty components and extremely complex machining operations.
SORALUCE FMT 4000, multifunction and total profitability
The SORALUCE FMT model is a multitasking centre of great size. Its power and torque in the universal milling head likewise full functionality on turning operations to enable the machining of very complex parts in a single set up. It is possible now to improve machining performance, this saving time and generating greater profitability for the user not only in serial production but also in unit production.
This machine has an innovative design based on a more flexible work area totally customizable according to each costumer´s particular specifications. That way, they can choose between one or several work areas likewise incorporation of rotary or fixed tables.
This model has a complete splash guarding that allows great accessibility, thanks to its automatic door opening with full frontal and upside access to the work area and facilitates the collection of chip and cutting fluid. To offer better visibility it has great glass surface. Ease of operation, cleaning and safety for a guarding that can be completed with a smoke extraction system.
SORALUCE SLP 6000, a well-designed machine: ergonomics and user friendly
The SLP 6000 fixed table travelling column machine is a large capacity machine designed in a compact and ergonomic format, offering great flexibility. The machine offers high precision finishing results, based on unique traditional machine architecture: table attached column supported by a separate rear guide, to improve machine stability, whilst maintaining its very low centre of gravity.
It is the ideal machine for sectors such as: industrial vehicles, moulds and dies, capital goods and medium sized work piece subcontractors.
The milling machine is equipped with the SORALUCE orthogonal head indexing at 1º x 1º, with its compact design specially conceived for machines with an in-line motor. This head enables the end user to take full advantage of machine travel: eliminating the need for additional work piece support fixtures, due to close to table head spindle accessibility for both front and lateral milling. An extra orthogonal head feature is that of machining inversely. The machine enables the orthogonal head to be positioned for inverse machining, up to -45º. This eliminates the need for additional setups, resulting in improved overall cycle times and finish quality with less component manipulation.
SORALUCE FL 6000, Dynamic and versatile
The SORALUCE FL milling and boring centre is a multi-purpose milling and boring machine offering exceptional versatility and enabling customers to increase their productivity.
It is the ideal machine for sectors such as industrial vehicles, moulds and dies, capital goods and medium sized work piece subcontractors.
It is a high dynamics machine with speeds up to 35 m/min and acceleration of 2 m/s2 in longitudinal, vertical and traversal axes, resulting from a combination of linear guiding and double rack and pinion driving systems. Working feed force of 16000 N on all axes.
High precision and efficiency provided by a high torque direct drive spindle motor, likewise also guarantees low heat, reduced noise and no maintenance.
SORALUCE FR-W 12000, high performance and robust machining
SORALUCE FR-W floor type milling-boring centre with modular quill offers high versatility and productivity for large component machining, becoming a multi-purpose milling boring machine.
It is the ideal solution for machining components belonging to sectors like: energy (wind-power, gas, nuclear), shipbuilding and capital goods, ensuring the highest precision, productivity and reliability for heavy duty components and extremely complex machining operations.
Its rigid stable design provides the highest precision and productivity benefits when machining large components. The machine offers high performance machining results thanks to its high dynamic driving system and a combined guiding and damping system besides offering the proven optimum in power and cutting speed capabilities, reaching up to 100 kW in S1.
The machine modular design offers remarkable versatility and can be equipped with a large number of optional accessories and wide range of milling-boring heads, enabling the machine to be adapted to customer’s needs with high efficiency and precision. Furthermore, due to the travelling column concept of the machine, it can be equipped with several working stations, thus enabling simultaneous machining and loading of different workpieces. The machine responds to multitasking and versatility requirements likewise the demand for finishing workpieces in a minimum number of set-ups.
Thanks to its flat longitudinal axis design and low profile column connection, the machine centre of gravity is kept very low, enabling high machine stability, reduced foundation costs, improved machine operation and ergonomic maintenance.
SORALUCE FP 8000, high versatility and productivity for medium and large size components machining
The FP milling boring centre is a multi-purpose milling- boring machine. Its rigid stable design provides the highest precision and productivity benefits when machining medium and large size components.
The machine modular design offers remarkable versatility and can be equipped with a large number of optional accessories and wide range of milling-boring heads, enabling the machine adaptation to customer needs with high efficiency and precision. It is the ideal solution for machining components belonging to sectors like: energy (wind-power, gas, nuclear), shipbuilding and capital goods, ensuring the highest precision, productivity and reliability.
Furthermore, due to the travelling column concept of the machine, it can be equipped with several working stations (floor plate, rotary table, rotary-travelling table, etc.) thus enabling simultaneous machining and loading of different work pieces.
The machine responds to multitasking and versatility requirements likewise the demand for finishing work pieces in a minimum number of set-ups.
TA-A 35, high capacity in a compact machine
The TA-A milling centre is a bed type configuration milling machine distinguished by its optimum stiffness and complete mechanical stability. It is notable for its long-lasting precision provided by a strict design and assembly process and high stock removal capacity.
It is the ideal machine for high precision mould and die manufacturers likewise medium sized high precision work piece engineering.
It is equipped with a total enclosure, which is compact ergonomic, and fully accessible from the front and rear for easy work piece clamping, measuring and operator access to the working area.
SORALUCE, Home of Innovation
SORALUCE invests 7% of its total turnover in research and development. Innovation distinguishes SORALUCE and it is the unique way SORALUCE develops and does things. SORALUCE has a "unique way of undertaking" innovation, based on their powerful innovation platforms:
There is an internal research and development department which collects customers’ and sales teams’ concerns and needs, thus maintaining close contact with the market. The central R&D department concentrates about 80% of resources on future technologies and new products.
SORALUCE develops the technologies of tomorrow together with its own research centre IK4-IDEKO. IK4-IDEKO, located in the vicinity of SORALUCE, has over 120 engineers and 24 doctors, leads innovation in the sector with intensive coo-operation with 40 international research institutes and universities throughout the world and has taken part in over 50 European projects.
The technologies developed are materialised and implemented in SORALUCE products, with a close monitoring of the production process. All these new technologies are transferred to the Centre of Excellence in Limburg, BIMATEC SORALUCE, where German engineers test the machines under the most demanding circumstances. The Centre of Excellence is the SORALUCE International technology testing centre and the SORALUCE Academy site.
This is how future technology is born in SORALUCE and how SORALUCE assumes technological leadership with its Home of Innovation. Technology born from listening to the market, customers and users.
This way of working has led SORALUCE to become a pioneer and mark on the market: setting new standards in milling, boring and vertical turning technologies.
The customers can be certain that when buying from SORALUCE they get the technology that they need not mention they are making the right investment, either buying a premium machine with the required customizations, or relying on SORALUCE to perform the most complex custom made projects.
SORALUCE, wide experience
The European brand has extensive experience with over 2,500 machines sold, nearly half of them in Germany, a highly demanding market. It has also been determined that over the years, 80 per cent of customers have trusted its products again.
SORALUCE is part of DANOBATGROUP, machine-tool division of MONDRAGON Corporation, one of the most important holdings in Europe. With nearly twenty top-level manufacturing plants in Spain, Germany, UK and the United States. It also has its own R+D centre with 120 engineers and 24 doctors. DANOBATGROUP provides one of the most complete and solid multi-technological offer on the market. In the last five years it has kept a turnover of about 250 million euros, enabling it to continue with a high investment in I+ D+ i, considering to approximately 6.5 % of its turnover.