SORALUCE thinks ahead to digital environments in milling, boring and turning
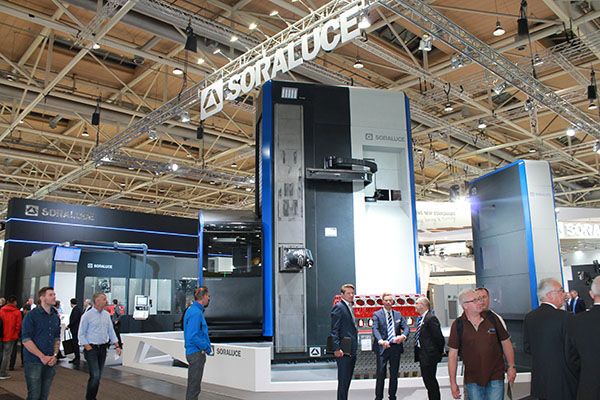
Inspired by innovation and with experience based on 55 years of history, SORALUCE is the worldwide leader in milling, boring and turning technologies. Innovation is at the forefront and many of the technologies that drive the machine tool sector have been pioneered by SORALUCE.
We live in a world in constant evolution. A world, where we are all expected to stand out. Greater production rates, higher accuracy, improved efficiency, enhanced performance, user-friendliness, ergonomics, safety and cost-effectiveness; all while reducing cycle times, downtime, consumption and emissions. This is the sort of progress that makes sense for SORALUCE.
With a strong commitment to technology, SORALUCE is the best partner, providing outstanding services and expert advice. It takes technology to the limits through constant evolution, to supply reliable solutions and a wide range of added value services.
Innovation in SORALUCE moves beyond mere ideas, it becomes real and tangible in products and projects that set new standards in milling, boring and turning.
EMO 2017 is the platform chosen by SORALUCE to share the innovations that will shape the future. A future developed for and with customers while generating value.
Think digital – The future is digital
The new digital paradigm in manufacturing makes the interaction between machines, people and processes easier. SORALUCE helps its customers to become more competitive by innovating in the field of industrial digitalisation, improving operational efficiency by connecting the machines to the cloud in order to enable a seamless production information flow and maximise the machines’ performance. The interconnection of the equipment and the possibility of obtaining and analysing data from machines, open up the path towards creating smart manufacturing environments.
SORALUCE takes its range of machinery and solutions to a new level of competitiveness, with high value-added services intended to increase the availability and productivity of the solutions that it offers. SORALUCE Digital is deployed in four main activities: Advanced HMI, Intelligent Components, Data System and Control System.
Data system
SORALUCE Data System is a machine data-driven analytics tool that extracts valuable insights from the machine-generated data and that monitors its status and condition to ensure that the running performance of the machining process is as high as possible. SORALUCE Data System is a powerful tool to maximise uptime and manufacturing efficiency.
SORALUCE Data System includes several features; among them, the display of the machine status in real time providing relevant information about the situation of the machining in progress. The tool generates reports regarding sensitive issues for the user such as production or process, energy consumption or the performance of the machining cycles. It helps to optimise the machining process variables through the diagnosis of key warning signs related to the maintenance of the equipment and thus increases the machine’s productivity and avoids unnecessary consumption. It also sends emails automatically in the event of a shutdown.
Using specific hardware and applying the latest Big Data and Cloud Computing technologies, SORALUCE Data System collects and stores significant data from the CNC, PLC and sensors built into the machine and turns them into useful information. SORALUCE Data System brings together a set of services based on machine monitoring and Big Data to analyse the machining process and machine behaviour. It enables users to connect to the system remotely and securely via mobile devices including laptops, smartphones and tablets, and to have access to all the relevant information of the machines, factory logistics systems or other machines in the production system taking customers to the realm of the smart factory. In addition, it allows the connection with other machines of the factory and also with different management software applications such as ERP, MES, GMAO, etc.
Advanced HMI
Regarding the human-machine interface for machine operation, SORALUCE has been working on defining friendlier and better environments in an Advanced HMI. CNC used to be a dull and locked environment with preset functions, coding and limitations to integrate new functionalities, but not anymore. SORALUCE has developed a complete set of utilities on the HMI of the Heidenhain TNC 640 in order to achieve a user-friendly interface by means of softkeys, customised diagnosis masks and helper graphics for manufacturing cycles. These utilities have been designed to ease frequent operations, to enable recovering procedures (indexing head, tool changer, pickup station) after machine interruptions, to empower diagnosis functions by personalised masks and to improve ergonomics.
This Advanced HMI developed by SORALUCE consists of new softkey tree and proper diagnosis screens; the integration of the manufacturer cycles in the programming interface of the CNC; a machine 3D modelling for the Dynamic Collision Monitoring; and finally, the Advanced Tool Management that has been adapted to offer the user a new and more attractive concept of tool management, far from the standard used until today.
As a reinforcement of its commitment to improve ergonomics and ease of use, SORALUCE builds in its machine the new Heidenhain screen based on touch technology. A series of APPs have also been developed and integrated to allow access to relevant information located in an external PC, such as 3D drawings, the operation and diagnostics handbook or a proprietary software tool for the calculation of the position of the head, known as INDEXMILL.
Think innovate – the release of DAS+®
When a vibration problem arises, it is usually difficult for the machinist to assess where the problem comes from. To solve the situation, sometimes the cutting conditions are decreased, sometimes the tool type is changed, or the clamping fixtures are further tightened. These measures are often based on a trial and error procedure and thus, valuable time is lost in the process and a compromise solution far from the best machining performance is finally reached in the most optimistic case. Keeping this in mind, it is very important to identify the specific source of the vibration problem in order to apply a proper response.
SORALUCE presented worldwide during EMO 2015 its innovative patented DAS® system (Dynamics Active Stabiliser). Dedicated to maximising the cutting capability of the machine with long ram overhangs (where the dynamic stiffness of the machine is weaker), the DAS® system increases the dynamic rigidity of the machine in real time, increasing the machining performance by up to 300 per cent. This reduces the classic regenerative effect of chatter while machining.
After this successful and revolutionary development of the DAS® system, which received the Best of Industry 2015 and Quality Innovation of the Year 2015 awards, SORALUCE now presents the DAS+® System, an evolution of the DAS® system which now includes new functionalities to be showcased at a world premiere during this EMO 2017.
DAS+® includes vibration level monitoring, detection of chatter as well as two different extra strategies to suppress chatter: the new spindle speed tuning and spindle speed variation functions. This new function monitors the machining process and runs an internal algorithm that looks for the best cutting conditions to increase the stability of a particular operation. In the event of instability, the algorithm considers the chatter and excitation frequency generated by the tool and selects the best strategy to overcome the problem, automatically activating the DAS+® system, selecting the optimal spindle speed where chatter is suppressed or introducing a continuous harmonic oscillation in the spindle during the machining process. The machine becomes an assistant for the operator which can concentrate on maximising the use of the machine’s capabilities.
DAS+® makes the machine more intelligent and increases the productivity and robustness of the process, achieving reduced cycle times, longer tool life, a significant improvement of the surface quality and reduced machine wear. It includes all the knowledge and experience of SORALUCE in the field of machining dynamics, for the benefit of our customers.
Think technology – automation, multitasking and large sizes
Automated solutions:
SORALUCE is able to tackle automation projects at all different levels, from a single machine with a simple pallet transfer control integrated in the CNC, to a flexible machining cell composed of multiple machines with workpieces and tools feeding systems managed by an Industrial PC to support very complex management software.
SORALUCE has developed a customised Control System software to manage the machining cell using the job list concept. All the elements that make up the cell: machines, workpieces, pallets, tools, CNC programs, etc. are integrated by means of this software, making the operation easy.
Multitasking solutions:
SORALUCE multitasking machines achieve the highest profitability in the machining of technically complex parts, including milling & turning in a set-up. This machine range makes it possible to perform different cutting processes including turning, milling, boring, drilling and tapping operations with a single machine. All this is possible now for multiple kinds of workpieces of different sizes and shapes with efficiency and precision. It reduces the number of clamps required and minimises cycle times and potential errors. A multitasking option enables complex components to be machined in a single set-up.
SORALUCE provides a full suit of multitasking capabilities by means of SORALUCE’s design of turning heads, tables and customer cycles, and the special multitasking head for multitasking operations, milling and turning, offering increased capability and functionality.
In addition, SORALUCE integrates a new software, called Chip Breaker, a smart solution to break long chips that eases chip removal. The turning process often creates long chips and traditional chip conveyor systems cannot deal with such chips, which leads to stoppages in production and requiring manual removal from the machine. The chip breaker uses the drives of the machine to create an oscillation that produces small chips which are easier to remove, thus reducing machine downtime and ensuring continuous production.
Large size solutions
Machining large components calls for specific machines capable of guaranteeing the maximum precision, productivity and reliability required to be competitive on the market, and this is the environment for the new SORALUCE PXG.
Nowadays, machines for components of this type need to be capable of handling extremely complex machining operations. The machine needs to meet multitasking and versatility requirements so as to maximise productive time and minimise set-up time.
In this context, SORALUCE presents the new SORALUCE PXG, characterised by its high capabilities. It has a working volume of 1000 m3 and weighs 500 t. The dimensions of the model presented are as follows: 19 m in length, 7.25 m clearance between columns and 7.3 m in height. Height is also configurable thanks to the 5 m vertical travel of the crossbeam. The SORALUCE PXG belongs to the range of large-sized gantry milling machines and completes the top end of the company´s PM, PMG and PRG gantry-type machine range.
This highly versatile model is designed to meet the machining requirements for a range of highly demanding parts used in the construction of machinery for the energy industry, the machining of marine and CHP motors and the general machining of large workpieces.
The SORALUCE PXG is a completely versatile multitasking solution designed to maximise productivity through its ability to handle milling and turning operations with the same machine. It provides the highest possible return in machining large workpieces with a high degree of technical complexity, and makes it possible to machine a range of shapes and sizes. Its distinguishing feature is its ability to handle different machining processes including turning, milling, boring, drilling and threading with efficiency and precision. To that end, it can be equipped with several milling and turning heads with automatic tool changing. The machine features the latest technologies and solutions which are innovative in the large-sized machine segment.
It has been provided with linear guides on the X, Y and Z axes, which provide certain advantages over conventional solutions such as hydrostatic guides. The linear guiding system avoids the thermal gradients caused by the flow of oil through the structure of the machine, ensuring better geometrical stability and substantially reducing the maintenance required.
The general performance of the machine has been analysed carefully by SORALUCE´s innovation & design teams, which have run multiple simulations to correctly characterise the different deformations caused by the displacement of the moving parts of the system. In light of the results of these analyses, SORALUCE has created and applied a number of devices that largely offset the deformations caused by the weight of those moving parts. One of these devices is the innovative Vertical Ram Balance system (VRB), patent pending. The system, which consists of a CNC-controlled electromechanical system, offsets the rolling caused by the torsion of the cross beam and the differential bending of the columns when the ram travels along the cross (Y) axis of the machine. The system ensures maximum precision in terms of the perpendicularity of the X & Y axes, whatever the working position.
The machine also has a new thermal monitoring system that checks for changes over time in all its structural components via a function built into the CNC. It also has the latest thermal compensation algorithms developed by SORALUCE.
The turning table is fitted with sensors so that a new function built into the machine can be used to help the operator to re-balance the weight of parts with asymmetrical geometries.
Think tailored – taking customers to a new level of competitiveness
The new range of SORALUCE products, services and solutions prove the commitment of the company to staying close to the customer. SORALUCE’s technology is at the forefront of the required solution, and is adapted to meet the needs of each customer. A wide range of products, solutions and services that allow SORALUCE to supply from an individual machine to a complete manufacturing line that integrates turnkey machining solutions.
SORALUCE offers professional advice in machining engineering with a team of highly experienced engineers who evaluate the production and machining processes of our clients and provide solutions to optimise them, improving overall performance, achieving improvements in cycle times, increasing productivity, efficiency, profitability, etc.
In order to fulfill the diverse needs of each customer SORALUCE offers a wide range of heads, standard and special, workstations and other options for an optimal configuration. The options available for customers are so diverse, that each machine becomes a unique and individual project.
HOME OF INNOVATION
SORALUCE is committed to active listening and maintaining a very close relationship with customers at all levels.
All this information and experience is analysed and processed at our R&D&i department, which works in direct collaboration with our technology centre, and which in turn is in contact with international networks of universities and other research centres.
This is where customers’ needs find solutions that combine the theoretical concepts of scientific research with the complex reality of milling, boring and turning technologies’ applications in real part machining.
From the theory to the lab and from there to the reality of the machines which are tested at our Centre of Excellence in Germany, BIMATEC SORALUCE where, together with the customers, highly demanding machining tests are carried out to validate the technology and the machining solutions in order to solve their specific needs.
This ecosystem is our Home of Innovation, which seeks to turn into reality the technology that will become tomorrow’s new standards, and where SORALUCE invests 8% of its annual turnover.
SORALUCE, Setting new standards in milling, boring and turning
SORALUCE is the worldwide milling, boring and turning technology leader. Throughout its 55 years of history it has continuously made innovative and pioneering contributions in engineering that have become industry standards. Customers recognise SORALUCE for its expertise in milling, boring and turning solutions, always geared towards improving the customer’s efficiency and productivity, and for its technological capacity to customise each product based in the customer’s individual needs, likewise generating turn-key projects, designing and setting up complete lines according to the quality, efficiency and cost parameters required by the investor.
The European brand has extensive experience with over 2,500 machines sold, nearly half of them in Germany, a highly demanding market. It has also been determined that over the years, 80 per cent of customers have trusted in its products again.
SORALUCE is part of DANOBATGROUP, machine-tool division of MONDRAGON Corporation, one of the most important holdings in Europe. It has nine top-level manufacturing plants in Spain, Germany, the UK and the United States, an Excellence Centre in Germany, BIMATEC SORALUCE, and its own R+D centre with 120 engineers and 29 PhDs and more than 30 years of history. DANOBATGROUP provides one of the most complete and solid multi-technological offers on the market. In 2016 it achieved a turnover of 260 million euros with a workforce of 1300, enabling it to continue with a high investment in R&D&i, amounting to approximately 8 % of its turnover.